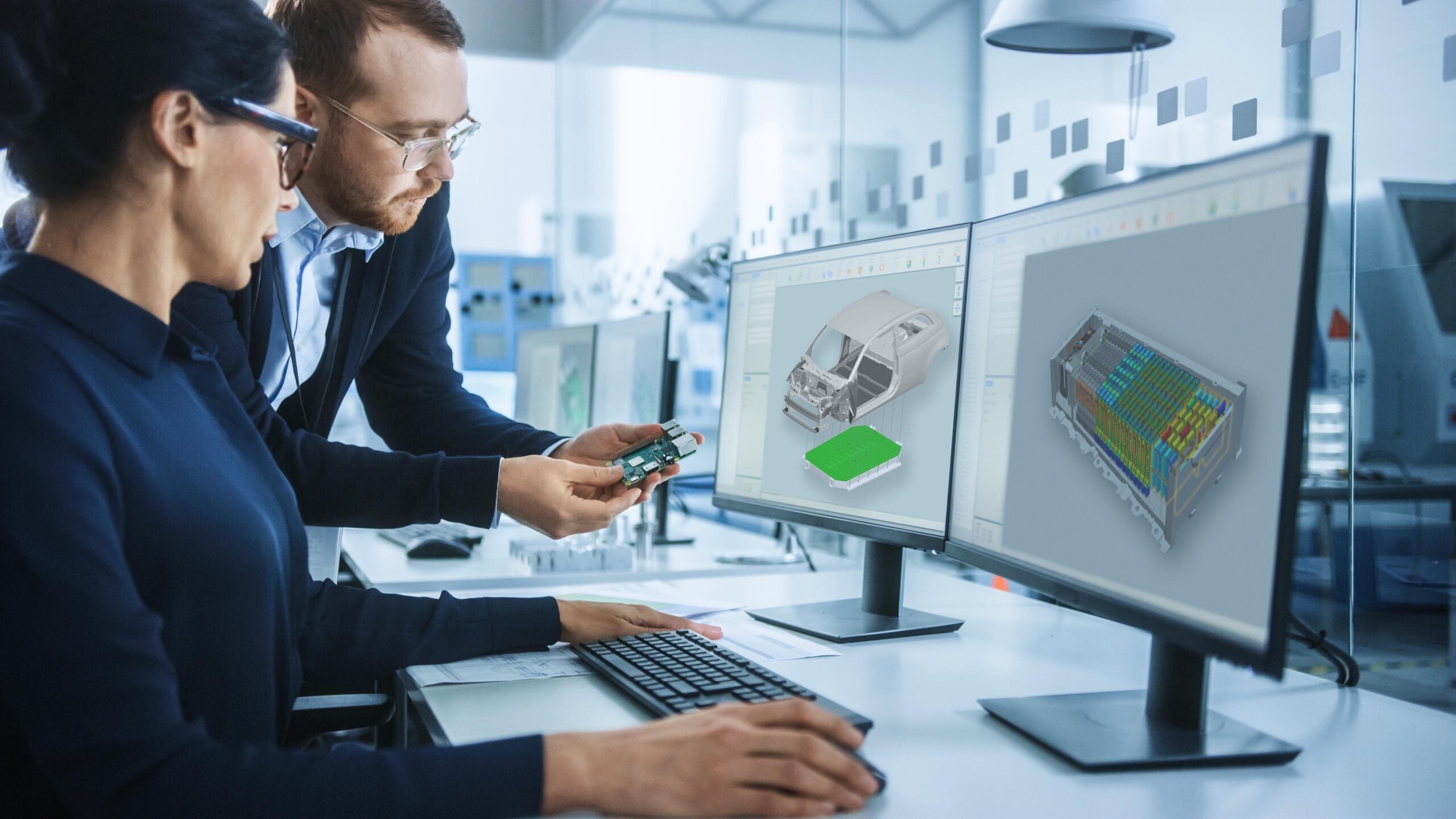
Cars have become difficult to live without, whether you love them with a passion or view them merely as a necessary tool. Therefore, the personal mobility part of the global response to the climate crisis, and the subsequent drive for Net Zero, has been to seek out cleaner cars, not to legislate them away completely.
After more than 100 years of cars powered by fossil fuels and internal combustion engines (ICE), the industry is looking to electricity for a sustainable solution. Many leading car brands including Audi, Ford and Volvo, have committed to being all-electric by 2030 or earlier. An analysis by Siemens Digital Industries Software suggests that the 2020s will be the decade of electrification. It suggests that by the end of the decade 58% of buses (up from 33% in 2020) will be electric, with 28% of cars and light commercial vehicles (up from 2.7% and 2%) and 40% of two-wheelers (30%) also electric in 2030.
The need to collaborate
However, engineering electric cars requires new skill sets and new ways of working that demand collaboration between engineering teams that, in the past, may not have typically collaborated. Collaboration is needed across the spectrum of teams involved in vehicle engineering, but especially between EV battery and body in white (BIW) teams.
BIW engineering teams are typically mechanical engineers with responsibilities including design of a car body that will meet performance and packaging constraints set out in the vehicle specifications. Packaging challenges include incorporating all vehicle components such as the interior, powertrain, electronics and storage space within the specified overall vehicle volume. The battery team primarily consists of electrical, electrochemistry experts, CFD and software engineers that are focussed on the performance of the battery pack. Their challenges are to make sure the battery systems can deliver the power needed to meet vehicle performance goals related to range and charging time, among others. In addition, the battery pack must operate in safe conditions from a thermal and crash standpoint.
In order to achieve the desired overall vehicle performance, the goals of the battery and body teams must be to cooperate and communicate on an ongoing basis throughout the design process. As these teams have not typically worked closely together on past ICE designs, and they do not necessarily share a common “design language”, this can pose challenges to achieving the desired level of efficient collaboration between teams.
“Year zero for EVs as a mainstream ICE replacement is considered by many to be 2008 – the year that saw launches for Tesla’s first Roadster, the Chevy Volt and the Nissan Leaf. The EV industry is therefore only 13 years into its journey into the mainstream. And while it has come a long way very quickly, it needs to meet new challenges all the time,” says Edward Bernardon, Vice President, Strategic Automotive Initiatives, Siemens Digital Industries Software.
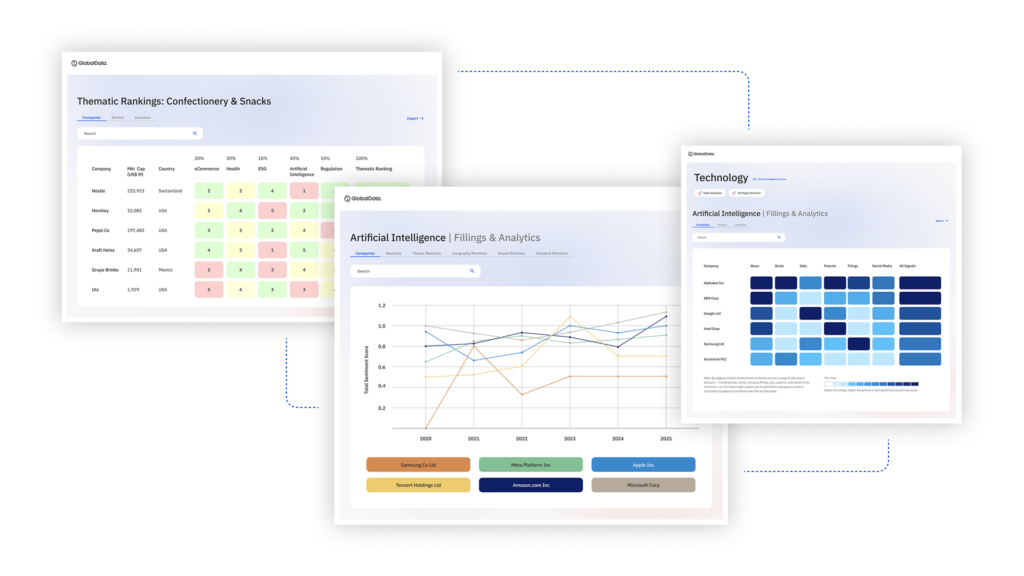
US Tariffs are shifting - will you react or anticipate?
Don’t let policy changes catch you off guard. Stay proactive with real-time data and expert analysis.
By GlobalData“You have two teams without a thorough understanding of the impact their design choices may have on the other team. As the typical powertrain configuration has been well established for ICE vehicles, the methodology for packaging the ICE powertrain is also well understood. With less consensus on approach for EV powertrain system integration, more parameters are in flux especially those related to battery systems integration into the car body,” says Bernardon.
Figure: 1: Comparison of body development for ICE and EV platforms.
Design and engineering trade-offs
While the cost, weight and volume of batteries used in EVs today remains far from ideal, the improvements in batteries getting cheaper, bigger and more powerful (60kWh to 80kWh), mean the major concerns today are less whether EVs are feasible and more a series of complex design and engineering trade-offs.
These decisions impact on – and are impacted by – both the battery and BIW teams and require a new common knowledge base. BIW teams need the input of a battery team, who can bring with them an understanding of battery technology and all the data that comes with that knowledge. At the same time, the battery team needs to consider how battery pack design choices might impact body design.
For the battery team, the solution to a problem like range anxiety may be to offer more range through more or larger batteries (or both). That presents design challenges to a BIW team, not least because batteries require space and add weight. The BIW team would like to reduce the number and size of batteries to make it easier to package the batteries with other systems and to meet structural and crash safety constraints.
Battery safety remains a key concern for consumers and EVs not only need a design that keeps passengers safe but a design that also protects the batteries during a crash, avoiding damage and the possibility of fire. Keeping batteries safe in a side impact collision can be challenging due to the limited space available, especially when batteries are located under the floor of the passenger compartment.
The challenge for car makers and designers is maintaining modern standards of comfort and safety – and convincing drivers they have achieved this – while either re-engineering existing vehicles or starting from scratch on a completely new design. Re-engineering a current ICE car into an EV may initially seem to be an efficient design choice, but it may be a more difficult design exercise with less freedom to innovate than embarking on completely new design.
To efficiently achieve the optimal EV design requires the two teams to collaborate, even though their goals may seem at odds. Indeed, not solving this organizational challenge can have a negative impact on the efficient development of an EV project. For as long as the BIW team works in isolation from the battery team; for as long as they continue to rely on two sets of data and deploy separate tools and systems to gather, manage and interpret that data; engineering processes will be inefficient, and outcomes will remain suboptimal. It is these barriers and separations that stand in the way of better outcomes.
The power of teamwork
“To work as effectively as possible, both parties need to think like a single team. When a design decision is made by the battery team the impact of that decision on the BIW team also needs to be evaluated as soon as possible. Otherwise, million-dollar decisions can be made without anyone really knowing it,” says Puneet Sinha, Director, New Mobility, Siemens Digital Industries Software.
Figure 2: The engineering process for battery pack and body in white (BIW) integration.
“A solution is to adopt a common engineering software platform and dataset that allows the battery team and the BIW team to work seamlessly together as they move on their journey of collaboration from initial concept to detailed design, to manufacture,” says Sinha.
Facilitating communication helps EV engineering teams more efficiently design vehicles that meet consumer demands for range, safety and reduced charging time. By sharing an engineering software platform based on a common data set, engineers can better understand each other’s design language, and efficiently collaborate to make the EV dream reality by designing and building sustainable EVs.
Further details:
For more information on technologies being discussed, click here.