Chrysler Group marked the extension of production, the addition of a second shift and an US$850m investment at an event at its Sterling Heights (Michigan) assembly plant which also celebrated the start of production of the extensively updated 2011 Chrysler 200 (nee Sebring) and Dodge Avenger.
“Today is a historic day for this facility. Not more than 18 months ago, it was slated to close at the end of this year,” said CEO Sergio Marchionne. “Now, this plant will not only remain open beyond 2012 and retain jobs, but with the help of the state of Michigan and the city of Sterling Heights, we will make a significant investment in this facility to make it competitive with the best in the industry.
The $850m investment included construction of a new 425,000 sq ft paint shop, as well as the installation of new machinery, tooling and material handling equipment. In addition, a portion of the total amount will be invested in the local stamping facilities in Warren and Sterling Heights.
With the announcement in July 2010 that the Sterling Heights plant (SHAP) would remain open beyond 2012, plant employees began working to transform the facility to build the 200 and Avenger, as well as future products, through the implementation of ‘World Class Manufacturing’ (WCM), an extensive and thorough process to restore all Chrysler Group facilities to their original and maximum functionality.
There already have been some tangible results in every model area where WCM has been established. In the body in white area, the left hand aperture stations had an 83% reduction in failures through the step-by-step process of restoring the equipment to basic conditions. With thorough cleaning and inspection activities, a similar result was achieved in the transfer station in the paint shop, improving throughput by 71%.
How well do you really know your competitors?
Access the most comprehensive Company Profiles on the market, powered by GlobalData. Save hours of research. Gain competitive edge.
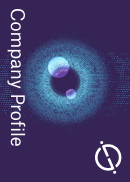
Thank you!
Your download email will arrive shortly
Not ready to buy yet? Download a free sample
We are confident about the unique quality of our Company Profiles. However, we want you to make the most beneficial decision for your business, so we offer a free sample that you can download by submitting the below form
By GlobalDataIn the past,the plant had experienced some surface defects originating in the paint shop colour booths. Using his WCM knowledge and the quality tools WCM provides, a team leader analysed, identified and resolved what had been a chronic quality problem, virtually eliminating it entirely and thereby, improving the exterior appearance for the customer.
The plant workforce has been generating hundreds of suggestions on how to further improve the manufacturing processes to ensure the highest quality vehicles roll off the assembly line. One suggestion involved the rebuilding of a weld gun pivot, which saved $5,000 per gun with an overall savings to date of more than $45,000. Team leaders have also generated more than 715 suggestions for improvement, which have helped the plant achieve the lowest three month in service warranty scores in the company.
“The employees have adopted the right mindset toward the implementation of WCM and are striving to reduce waste in everything they do,” said plant manager Tyree Minner. “As a result of their participation in this process, the team has saved more than $10m year to date and we are on track to exceed our total year end goal.”