Toyota’s Takahiro Fujioka has got something most auto plant managers would kill for right now: assembly lines running at almost full capacity.
The two lines at Fujioka’s Tsutsumi assembly plant in Toyota City, Aichi Prefecture, Japan, are rated at one vehicle every 65 seconds and 55 seconds respectively and, when just-auto visited a few days ago, the line rates were 66 and 57 seconds. That’s around 850 and 1,000 vehicles a day.
Unlike most Toyota plants in Japan, Fujioka’s two-shift operation has no non-production days in the schedule, still has some temporary workers (about 10% of the payroll), began working overtime again in April (just 15 minutes a day, as suppliers cannot provide enough parts for any more) and has even brought some workers up from the premium Lexus plant in Kyushu to meet demand.
The reason: the redesigned Prius hybrid which became Japan’s top selling car in May (tipping the rival Honda Insight off its April perch) and is currently being rolled out in export markets worldwide. Also due on the line any day now is an updated version of the previous Prius, called the EX, which will be sold only in Japan.
Line one was building North America-bound Prius models the day we visited, along with an occasional Scion tC, also for America, and a few Premio and Arion sedans, essentially high-spec domestic market versions of the Corolla.
How well do you really know your competitors?
Access the most comprehensive Company Profiles on the market, powered by GlobalData. Save hours of research. Gain competitive edge.
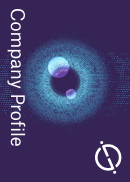
Thank you!
Your download email will arrive shortly
Not ready to buy yet? Download a free sample
We are confident about the unique quality of our Company Profiles. However, we want you to make the most beneficial decision for your business, so we offer a free sample that you can download by submitting the below form
By GlobalDataLine two rolls out domestic-spec and other export market Prius and the odd Japan market Camry while the new EX version of the old Prius for Japan will be squeezed on here soon.
Every two Priuses from Tsutsumi is supplemented by one built alongside domestic Noah, Boxy and Estima models at a Toyota Auto Body plant elsewhere in Japan; total hybrid capacity is around 50,000 a month.
For now, apart from CKD assembly in China (the kits are also made at Tsutsumi), there are no firm plans to build the Prius anywhere else; US production is likely only once demand there picks up sufficiently.
Encouraged by the Japanese policy of ‘kaizen’ or ‘continuous improvement’, Tsutsumi workers have come up with a couple of ideas line team leaders were keen to show the foreign visitors. One is a chair that enables an operator to swing effortlessly into a Prius, gear selector console at the ready, leaving both hands free to install it in seconds.
The other is a clever way to help new workers pick exactly the right number of bolts, lock washers and nuts from line-side trays for a particular operation.
Inserting the appropriate fastening tool into its holder on the parts trolley activates a mechanism that dunks little cone shaped magnets – the number above each tray corresponding to the quantity of fastenings needed – into the parts bins and fishes out just the right number of each, ready for the operator to grab and install.
There’s also a tyre label dispenser linked electronically to the production sequencing computer that illuminates the correct tray containing labels for the model and destination market of the car going by at the time.
Toyota officials were keen to stress that building hybrids requires no special dedicated assembly line or equipment – the Prius battery pack, with attendant cooling ducting, goes in behind the rear seat like any cabin component, the special orange-coated high-voltage wiring as easily as the main loom and the inverter pack, with coolant circuit, in under the bonnet just like any other engine bay part. The main extra helper we saw was a special lifter to help the operator guide the heavy battery pack on to the rear floor.
The only other line change for the new Prius is a halogen lamp tester in the quality control bay where the ends of the two assembly lines converge – these ensure the optional solar roof panel, which powers a ventilation fan when the car is parked, is operating properly.
All vehicles also benefit from a new sound insulation booth where completed cars are checked for door opening/closing and the functioning of interior items such as window winders and seat adjusters. A soundproof wall isolating this from the rest of the plant, glass wool ceiling and polycarbonate side walls have reduced noise levels from 75dB (roughly the equivalent of a city intersection) to 65dB (a residential street), enabling inspectors to better hear any annoying squeaks or rattles before the customer does.
Tsutsumi was opened in 1970, when environment concerns were not as high on the agenda as today, but a considerable amount of work has been done since the mid-1990s to make it as much of a ‘sustainable plant’ as possible.
Boiler upgrades have reduced CO2 output by 26,000 tonnes, for example, zero landfill and incineration waste has now been achieved and the water recycling system is so efficient it can supply a koi carp pond in a newly developed Japanese garden in the visitor reception area.
Employees have planted 55,000 trees in and around the plant, vines grow up the walls of buildings along the main entrance driveway, and drab, grey industrial building finishes have been replaced by light green, ‘photocatalyst’ paint that removes pollutants from the air. Solar panels line the roofs of the assembly and CKD kit packing plants and all the street lights around the facility are also solar-powered.
Graeme Roberts