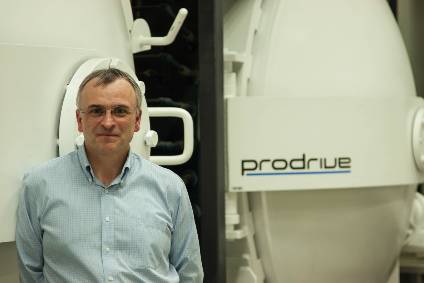
Prodrive Composites has developed a process for manufacturing recyclable composite components that can satisfy future end-of-life requirements without compromising the performance of the original parts. To learn more, we caught up with John McQuilliam FIMMM, Chief Engineer at Prodrive Composites and board member of the British Composites Society.
Could you explain a little more about the type of projects Prodrive Composites is working on?
A majority of our work is producing both functional and aesthetic carbon fibre components for UK automotive manufacturers. These range from carbon packages on SUVs to doors for hypercars; the diversity of parts we create here surprises most visitors. Behind the scenes, however, we are constantly working on ways to improve our production efficiency and part performance. Innovation in composites processes is the future of the industry and the lynchpin to dramatically broadening the applications for materials like carbon fibre.
It is not enough to develop a process for mass production if you do not have a plan for the carbon parts once they are no longer required.
With new processes we could reduce cost and bring things like carbon monocoques to the average mid-size SUV. I am not saying this will happen anytime soon, but I think we can all see the potential efficiency benefits of such widespread carbon fibre usage. It is important to note that while investigating processes that enable mass-production, we are also conscious of the need to consider end-of-life applications and recycling. It is not enough to develop a process for mass production if you do not have a plan for the carbon parts once they are no longer required.
For some time, carbon fibre has been used in F1, aerospace and marine applications and is gradually making its way into vehicle manufacture. Where do you see the greatest opportunities/applications for carbon fibre in mass produced cars?
Lightweighting is a well-established part of the industry's drive towards efficiency and composites manufacture has the potential to play a crucial role. Many high-end automakers are using carbon fibre extensively and this will inevitably lead to a drip-down effect of more widespread utilisation of the material. Use in mainstream production is still selective; some examples being BMW's i range and Carbon Core in the 7 series, as well as the new Toyota Prius' rear hatch. We know that the material is ideally suited to automotive applications and it's possible to build an entire vehicle with it – as many manufacturers already do.
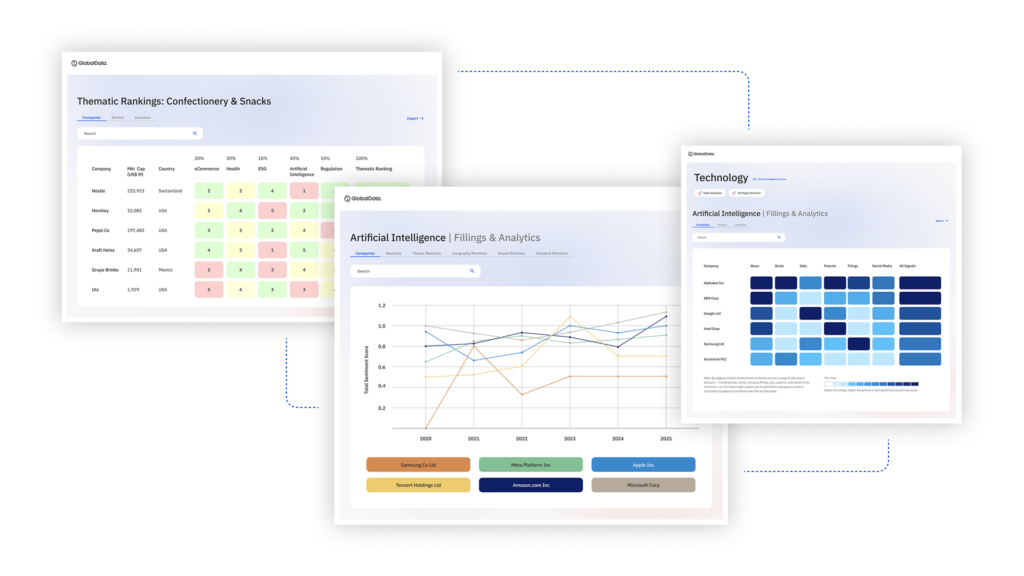
US Tariffs are shifting - will you react or anticipate?
Don’t let policy changes catch you off guard. Stay proactive with real-time data and expert analysis.
By GlobalDataUnfortunately, we still need to make considerable progress to reduce cost and improve manufacturability before we will see it in something like a Ford Focus. For now, the primary automotive market for carbon fibre is in high-end luxury and sports cars, which are using it more than ever. Perhaps with the knowledge we have gained from those vehicles, we can simplify part geometry and sacrifice some performance for cost, to reach a stage where the components are almost suitable for mass production.
It appears that processes to manufacture carbon fibre have moved faster than those for recycling it. Are there still challenges when it comes to end of life recycling of carbon fibre parts?
Recycling of conventional carbon fibre is still a challenge. Traditionally, the resin can be burnt off and the fibres chopped for re-use in non-structural applications, but even then, it is somewhat limited. However, at Prodrive Composites we have recently developed a manufacturing process called P2T (primary to tertiary) that emphasises recyclability and avoids the need for an autoclave. As it does not require heat or pressure costs are reduced, and it is possible to scale up production without major investment. The most interesting part is that we have retained similar mechanical performance to a conventionally made carbon fibre part. The idea is to not only simplify the process, but also give the raw materials three or more useful lifetimes. We have already produced parts using this process and it looks to be very promising indeed – simultaneously addressing scalability, ease-of-manufacture, performance, cost and recycling.
Can you envisage cheaper, easier-to-form alternatives to carbon fibre?
There is a trend toward lower cost and more sustainable fibres. Most carbon fibres are PAN based (polyacrylonitrile) fibres, made using a complicated heat treatment process, but people are now looking for alternatives. That is, alternative methods of producing PAN fibres and also completely different fibres, including natural sources such as flax. Using natural fibres can also be seen as a means of carbon capture, because when grown they are taking carbon dioxide from the atmosphere and forming carbohydrates, locking it away.
A lot of carbon fibre work is currently done using continuous fibres, but there is now a trend toward using long fibres. Long fibres offer virtually identical strength and fatigue properties as continuous fibres. This opens doors to new manufacturing processes like pressing where the fibres are able to slide over one another to avoid breaking. Further resin development, including the use of thermoplastics, will also reduce cost and improve the ease of production.
What new and potential automotive applications are there for composites?
Wheel development is a traditionally neglected area. Wheels are rotating and un-sprung mass, so making them lighter will have a significant effect on performance and economy. While there are carbon wheels available on high performance sports and racing cars, we should seek a simpler and more economical design for use in high-volume applications. A perfect candidate would be EVs, as regenerative braking produces less heat than conventional braking systems. Granted most current EVs also have conventional braking systems, but these are used as a backup and not the primary system that they are on conventional ICE cars.
Increased structural use of composites is on the horizon.
Increased structural use of composites is on the horizon. The major players are well established in the use of metals and this is one of the main factors holding back wider use of composites in the automotive industry, as well as a sense of risk aversion. It is very similar to the way aerospace was 30-40 years ago. Non-structural applications, including vehicle interiors, is another excellent opportunity for the use of composites.
Which automotive applications are the most promising for 'smart materials'?
The additive nature of composite manufacture means that it is quite easy to incorporate things like wire looms, sensors or fluid channels. As you can imagine, the possible applications are extensive and by providing an increased level of functionality you can offset some of the cost. The high strength and fatigue properties also make it suitable as a 'living hinge', flexing to provide aerodynamic or cooling benefits.