Reducing total cost of ownership and ensuring that new lightweight steels are strong enough to protect vehicle occupants in a crash are key challenges for materials and car designers alike. To find out more, Matthew Beecham spoke to Chris Wooffindin, Tata Steel's product marketing manager for automotive.
Could you explain how advanced steels have the potential to lower the total cost of ownership of the user?
The concept of Tata Steel's Total Cost of Ownership (TCO) is that vehicle lightweighting must be cost effective. The automotive industry is a competitive one and our customers constantly face the paradox of achieving optimum performance at lowest weight and at lowest cost. The adoption of non-steel material to achieve lightweighting often comes at a significant cost premium.
At Tata Steel we believe that the optimal application of advanced steels can help our customers achieve their goals and targets. Lowest total cost of ownership refers to the aim to meet these goals and targets at lowest final cost to our customers. When developing lightweight solutions, we review the total cost from mother coil through to final assembled cost as many cost parameters can change, not just the difference in material grade. Lowest TCO also refers to the smart application of advanced steel grades which might extend beyond lightweighting to also improving press-shop efficiency.
Tata Steel has developed a new engineering service called TCO scans. This service enables Tata Steel automotive engineers to work with the customer to prove where the application of our advanced steels sits in the balance between performance, cost and weight.
One example is a TCO scan using our new chassis grade currently in development, XPF800. We demonstrated the replacement of complex phase 800 in the chassis lower control arm with XPF800 can yield a ten percent weight reduction, minor performance improvement and a lower final cost.
How well do you really know your competitors?
Access the most comprehensive Company Profiles on the market, powered by GlobalData. Save hours of research. Gain competitive edge.
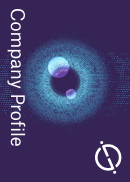
Thank you!
Your download email will arrive shortly
Not ready to buy yet? Download a free sample
We are confident about the unique quality of our Company Profiles. However, we want you to make the most beneficial decision for your business, so we offer a free sample that you can download by submitting the below form
By GlobalDataAnother example unrelated to lightweighting, but relevant to lowering our customers TCO, relates to our Magizinc product. A recent customer TCO scan demonstrated that replacing conventional galvanised (GI) coated steel with Magizinc resulted in 30 percent less tool pollution. This meant that our customer was able to increase the press-shop efficiency, which resulted in significant cost savings.
To what extent can formability contribute to lightweighting and which automotive applications / areas offer the greatest opportunities?
Increased formability is a key enabler to achieving lightweighting. A common way of achieving lightweighting is to use the so-called upgrade – downgauge principle. This is especially applicable for components that are strength dominated such as safety cell reinforcements or chassis components such as the lower control arm. By using higher strength material, the engineer can achieve equivalent strength whilst specifying a lower thickness, which leads to a lower component weight. However, in general terms, higher-strength material, especially conventional high-strength steels, have lower formability. This means that the final component shape might be challenging to produce without material rupturing. The steel industry continues to develop new steels offering both high strength and improved formability to address the need for lightweighting whilst reducing the impact at the press shop.
Are there certain grades of steel being used for certain front and side impact applications?
The steel industry has developed a range of advanced and ultra-high-strength steel grades to meet the different performance demands within the vehicle structure. Safety reinforcements at the front of the vehicle need to absorb energy during frontal crash. Safety reinforcements in the so-called passenger safety cell needs to prevent intrusion to protect vehicle occupants during all crash events.
For front-end safety reinforcements, such as the longitudinal reinforcements, it is common to see the application of dual-phase AHSS [advanced high-strength steel] grades. This family contains different strength levels but commonly features relatively low yield strength and high tensile strength leading to good forming properties. This family of steel also features many benefits during a crash, but the most important is the high strain rate sensitivity. This means that the faster the material is deformed, the higher the amount of energy is absorbed making it very efficient for front crash geometry.
Safety reinforcements in the passenger cell need very high yield strength to minimise deformation during crash events. There are different steel solutions depending on the application, design and budget. Complex phase steels feature very high yield and tensile strength with forming characteristics making them suitable for roll-formed components such as tunnel reinforcements, sill reinforcements and roof bows.
The use of hot-formed boron is now ubiquitous in Europe for safety-critical components found in the passenger car safety cell. These grades have the strength and formability of mid-strength micro-alloyed high-strength steel in cold form. However, after heat treatment, for example during the hot-stamping process, the final strength is often beyond 1500MPa, more than tripling in strength. This enables the engineer to design components with extremely high strength and therefore excellent bending strength to minimise passenger cell intrusion during all major crash events.
Are there any performance benefits that your steel technology offers the bumper beam structure that are not achievable with standard steels and aluminium?
The optimal material selection for bumpers beams very much depends on the design and preferred manufacturing methodology. For example, rolled-formed bumper beams will benefit from the application of complex phase material. Complex phase material couples very high strength with good bendability and edge expansion making it ideal to produce a very efficient structure using the roll-forming process. For more complex designs or designs where the shape requires press-forming, assuming very high strength is needed then hot-stamped boron is an ideal match.
High strength steels are under continual development but how does, say, ultra high strength steel compare to aluminium? Are there challenges with the efficiency and performance consistency of thin-walled steel structures?
Ultra-high strength steels (UHSS) offer lightweighting benefits over aluminium, especially for package-constrained safety reinforcements. UHSS steel is much stronger, with a three times higher Young's modulus than the highest aluminium grade currently in the automotive market. Many UHSS safety reinforcements need very high bending strength.
An example is the B-Pillar reinforcement, a critical lifesaving component during side impact. When the B-Pillar is impacted the component must initially resist bending with the next phase needing very high strength to minimise deflection and rupturing. The package space – the volume in which the component can fit – is very tight due to the need to maximise the door openings and interior space. Aluminium is less efficient in terms of stiffness which means that the component will deflect sooner and as it has a lower strength, the ability to resist deflection and rupture will be much less than for UHSS steel. UHSS steel grades therefore have a clear advantage over aluminium for such applications.
Thin-walled structures can offer challenges to design and manufacturing engineers. As previously mentioned stiffness is important for many components in the car. Reducing the material thickness will negatively affect stiffness so the engineer must recover any loss in stiffness through shape design. If there are limits to which the extent of shape can be altered then there are many techniques to help stabilise the thin-walled geometry. Examples include joining or welding technologies or even the use of foam filler to support the section.
To what extent are you working with other companies to develop ultra high strength steels?
The remainder of this interview is available on just-auto's QUBE Global vehicle lightweighting – technology, trends and the future