The rise of computer processing power together with the introduction of so called 'supercomputers' have enabled computational fluid dynamics (CFD) – the prediction of fluid flows using mathematical modelling – to become increasingly relevant and effective in road vehicle development. Matthew Beecham spoke to Rob Kaczmarek, director of marketing at Convergent Science about the role of CFD in vehicle development.
Can you tell us a little more about Convergent Science?
We are a world leader in the development of CFD software with specific class-leading expertise in engine simulation. You have probably seen lots of those coloured images described as CFD models. CFD is about developing an insight into flow patterns from liquid or gases that are difficult or expensive to study using traditional techniques. Our founders are specialists in engine simulation and, having been frustrated by the issues that they encountered using other programmes, they created Convergent Science in 1997 to develop an effective CFD tool to solve the problems they were having with the current state-of-the-art tools at the time. With specific expertise in liquid spray, combustion, flame propagation and emissions formation and each having a background in engine development, our founders were able to produce a tool that was ideal for engine simulation with time saving features that were not found anywhere else. Today our headquarters are in the US with offices in Wisconsin, Texas, UK, Austria and we have additional distributors in Japan, China, and India. We have just opened our newest location in Linz, Austria serving the growing number of European customers in both OEM and motorsport applications.
What is driving the growth of CFD?
The key drivers are the real and substantial gains in cost and time that can be achieved. Simulation, in our case primarily concerning the powertrain, is now a cost-effective and viable alternative to real world testing. A fully instrumented engine test stand is expensive – probably £1m plus all the running costs. CFD can minimise the need to use these at every stage of engine development and avoids the requirement to test every 'case'. The other benefit is the significant time saved and this is one area where we are particularly strong. One European OEM told us that since they started using our CFD programme, 'Converge' its productivity had increased by ten times in the last two to three years. It allows them to assess and test many more engine cases to find the optimum design and engine setting as well as minimising prototypes. That same European OEM says it can now run 7,000 cases a year. This is a really great testament to our automated meshing process, which adaptively refines at runtime, allowing for an effective use of time compared to say, ten years ago.
So how has CFD changed over the past decade?
How well do you really know your competitors?
Access the most comprehensive Company Profiles on the market, powered by GlobalData. Save hours of research. Gain competitive edge.
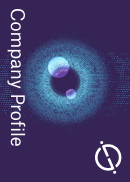
Thank you!
Your download email will arrive shortly
Not ready to buy yet? Download a free sample
We are confident about the unique quality of our Company Profiles. However, we want you to make the most beneficial decision for your business, so we offer a free sample that you can download by submitting the below form
By GlobalDataWhat has really enabled CFD to take off in engine development is the rise of computing power and fully coupled automated meshing. Meshing was the biggest issue for a lot of engineers ten years ago. Having confidence in your finds was difficult knowing that if you changed the mesh the answer was going to change as well. Now we run grid-convergence studies to find the optimal mesh size for a given configuration and run a full sweep of analysis. Having confidence in the mesh now allows CFD to be used in a much more predictive role than just a few years ago. Also the availability of multi-core machines as desktop computers and the ease at which organisations can access cluster or cloud computers means more companies can use CFD and design optimisation has become a reality. Some 10 to 15 years ago, CFD was really only capable of doing very simple analysis, and there was a huge difficulty to resolve the flow around moving parts.
Now with advances such as in our Converge product, software that fully couples and automates the mesh at runtime, it has enabled CFD users to save weeks in development time and eliminated that user-to-user variation inherent in the traditional approach. Where companies have switched to our software, CFD is now being embraced because of their confidence in the results. CFD use is rising and the number of areas where it is now being used is also expanding.
Could you provide such examples where OEMs are looking to use Converge?
Converge can be used for any flow – fluid or gas and moving parts or no moving parts the setup is just as easy. Because our founders are true engine specialists, OEMs place real value on that expertise and it is where we think we are adding particular value in the automotive sector. Good examples include looking at liquid atomisation, flame location and increasingly, emissions. Converge is very successful at predicting trends in emissions for a given design. That really helps OEMs to define the optimum parameters of a powertrain before cutting any metal or getting anywhere near the test track. That probably explains that the push to switch to Converge is initially a grass roots campaign from the engineers whom are fed up with meshing and senior management relish the cost savings and the confidence they can provide with it.
Who are the customers using your software?
Confidentiality prevents me from mentioning all our customers but we work with all the key US OEMs and a number of these have global licences, so we also support their subsidiary brands in Europe and the Far East. We have a growing number of European OEMs and all but a few of the Japanese and Korean OEMs in the passenger car sector now are utilising Converge. We are working with F1 and other professional motorsport teams. We have customers in the heavy diesel sector such as Cummins, CAT and a number of European Tier Ones and Tier Twos. We have recently started a venture with IFPEN, a public research body covering the fields of energy, transport and the environment. We will work together to broaden the combustion modeling capabilities available to the worldwide automotive industry. We are really excited and this partnership moves us a little closer to one of our aspirations to create fully predictive CFD.
You talk about rising numbers of European OEMs using Converge. Why are they switching to you?
The industry always believed a fully coupled automated mesh that adaptively refines to a user's specifications at runtime was a kind of Holy Grail and other versions out there had failed to deliver. A NASCAR customer told me he thought he would never see an effective version in his lifetime but we have actually done it. By generating the mesh at runtime you eliminate the variation between different engineers and the subsequent disparity and error in results otherwise inherent. And with the mesh adaptively refining at runtime you put the added mesh resolution where it's needed, when it's needed. After seeing so many promises and failures from other suppliers there is an initial scepticism, but once they try our software and see that it really can generate an extremely accurate mesh and has great runtimes without creating a mesh manually, they want to work with us. The engineers like it because they can spend more time designing, working through problems and finding better solutions. Of course our free version, Converge Lite that is coupled into Gamma Technology's GT-SUITE doesn't hurt our case either.
If you have solved the issues of user variation and are saving time, what or where are the next gains going to come from?
The remainder of this interview is available on just-auto's QUBE Global light vehicle engine technologies market- forecasts to 2030