Is Toyota’s much vaunted supply chain management system on the verge of meltdown in the midst of the unfolding quality crisis centred on faulty accelerator pedals? SupplierBusiness reports
The global quality crisis now hammering Toyota has launched a debate about whether the blame should be placed squarely on the company’s renowned system of supplier relations. At the very least, supplier executives say Toyota may be ready to reevaluate its method of early involvement and close, long-term partnerships with individual suppliers, as well as single-sourcing, in the wake of plans to modify or replace millions of faulty accelerator pedals around the world.
Is ‘The Toyota Way’ still the right way for a company that has grown so much in the past decade? Several schools of thought emerged in the days following last week’s disastrous turn of events. Among them:
- Toyota’s deeply integrated ties with its parts makers actually permitted the problems with the pedal modules to occur. How? The automaker has remained lean while its volume has increased dramatically since the days when the company’s principles and methods were established. Thus, Toyota can no longer maintain sufficient support and quality control, especially as it adds new suppliers around the world. Yet it still governs the design of key components.
- Toyota’s streamlined supply base is at fault. By relying so heavily on sole suppliers and using parts across multiple platforms and vehicles, the automaker increases its risks.
- Toyota’s methods have minimised the damage – enabling a relatively quick fix to the sticky pedal problem because of the automaker’s inherent ability to work closely with suppliers on engineering solutions.
But the consensus among analysts is that Toyota’s rapid expansion is at the core of the problem. They say the company can no longer maintain the same level of quality control and engineering rigor. And they say Toyota has rushed into relationships with suppliers it has not adequately vetted, shifting away from trusted Japanese-based companies in favor of new parts makers located around the world.
The automaker has also been forced to slash costs as part of its growing orientation towards stock market performance that followed its listing on the New York exchange in the late 1990s. Also, Toyota’s recalls have involved fantastically large numbers of vehicles, which some critics say is the result of reliance on single suppliers that provide common components for many platforms and vehicles. The lack of a second supplier means it can’t easily switch sources.
For CTS, it has been a sharp learning curve. Last week, the executives who run the half-billion dollar company might have been rethinking the wisdom of diversifying into the auto business five years ago. It has been exposed to the terrors of manufacturing high-profile products that are sold to millions of consumers.
CTS might have felt secure in the fact that its first automotive customer was Toyota. The components were engineered to Toyota’s design. Toyota spokesman said, “Our position on suppliers has always been that Toyota is responsible for the cars.”
The recall has increased CTS production, as it grinds out the replacement parts it has already begun shipping to Toyota assembly plants. CTS will also benefit from the Toyota manufacturing experts now entrenched in the supplier’s three factories to help speed production. That ought to yield long-term efficiency benefits to CTS. And the deep ties now being forged to Toyota could help assure future business.
Toyota looks to be doing the right thing by not turning CTS into an adversary in the crisis, as happened in the infamous Ford-Firestone recall in 2000. But CTS initially took issue with Toyota’s claim that its pedals could be a source of unintended acceleration. CTS said that while reports of runaway Toyota vehicles went back as far as 1999, it did not begin making pedals for the company until the 2005 model year.
CTS executives seem to wonder why their component is being connected with Toyota’s overall unintended acceleration crisis at all. They say there are not aware of any crashes or injuries caused by one of its pedals becoming stuck.
So the question arises: Despite the apparent cooperation between automaker and supplier has CTS been left to twist in the wind?
Toyota’s recent problems certainly underscore how certain elements of its approach, including the cost-saving practice of using common parts and designs across multiple product lines, and reducing the number of suppliers to procure parts in greater scale can backfire when quality-control issues arise.
Whatever happens next, life has changed to one degree or another for Toyota suppliers in the past year. Production is down, Toyota has asked for price reductions and a new supplier quality offensive is sure to emerge from within the company. The next crop of supplier surveys that grade relations with the OEMs should be fascinating.
This article was supplied to just-auto by SupplierBusiness, an IHS Global Insight company.
BELGIUM: Toyota to repair up to 1.8m European gas pedals
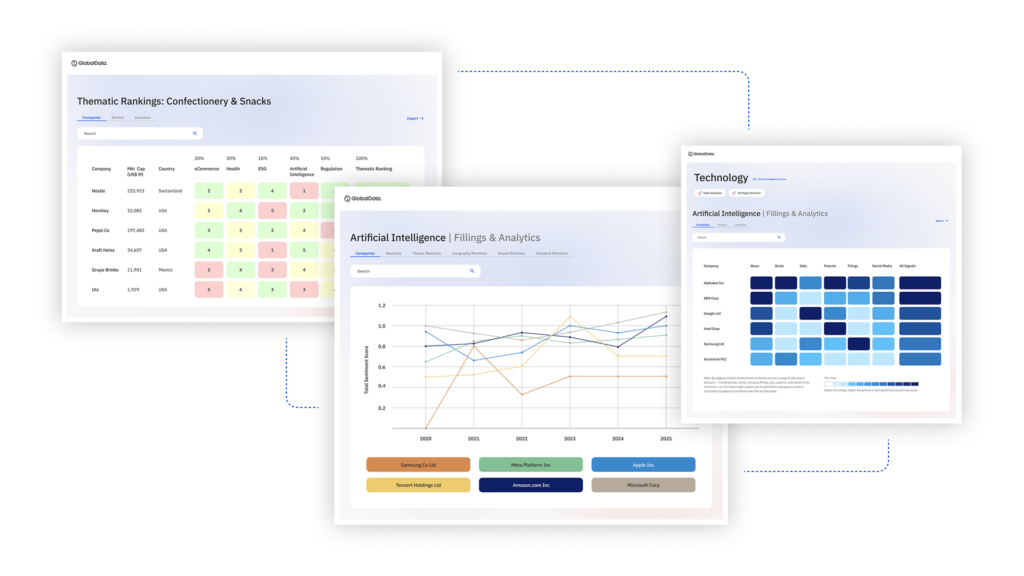
US Tariffs are shifting - will you react or anticipate?
Don’t let policy changes catch you off guard. Stay proactive with real-time data and expert analysis.
By GlobalData