
Vehicle designers and engineers are coming under unprecedented pressure to remove weight from vehicles wherever they can. As part of a new research project from just-auto/QUBE, Matthew Beecham considers aspects of the challenge to remove weight from vehicles.
For some time, the automotive industry has been under pressure to change the way it designs and builds vehicles, due to factors such as the increasing impact of passenger and pedestrian safety requirements and the competitive intensity caused by globalisation and manufacture in low cost economies. Governmental pressure in Europe and North America to reduce the CO2 emissions has also prompted automakers and their supply base to develop automotive technology to meet those strict emission limits. Consequently, more and more vehicles are incorporating components aimed at mass reduction, parts consolidation to reduce assembly costs and more efficient recycling. The automaker’s need to improve overall fuel economy in vehicles has led to the trend toward minimising vehicle weight. The use of performance materials such as high strength steel and aluminium is on the rise and heavier traditional materials, such as steel and iron, are being replaced whenever possible.
The VW Golf VII is a prime example of the trend for lightweighting, weighing in at 100 kg lighter than its predecessor. The latest generation Golf offers a carbon fibre roof as an option on performance models. The roof saves approximately 9 kg which clearly helps to improve performance and fuel economy. This move further demonstrates how far the use of carbon fibre in vehicle manufacture has come. Indeed, it is no longer the preserve of the luxury class but could soon become more commonplace in mid-range segments. The car body itself is estimated to be 37 kg lighter than the last generation Golf. The weight loss here is due to the use of new materials and manufacturing processes, including the use of laser stir welding, also known as the ‘wobble method’.
Next generation models are expected to shed even more weight. For instance, the Ford Mondeo concept weighs in at 1,195kg, equivalent to the current diesel-powered Fiesta. The concept features parts such as carbon fibre seats and 19-inch wheels, high-strength steels, aluminium in the chassis and composite springs for the front suspension. The net result of such efforts to reduce vehicle weight are faster acceleration and improved fuel economy over the 31.4mpg offered by today’s car.
While switching the use of materials for such major components represents the bulk of the weight savings on the Golf VII and Ford Mondeo, there are other small but important measures that have been applied to the latest Golf. For instance, during an interview with just-auto, Bernhard Rosenau, Segment Management Automotive, Engineering Plastics Europe, BASF SE, talked about some of its most recent PA and PU automotive applications. More specifically, BASF has helped Volkswagen to save weight and cost from the latest Golf’s front-end carrier. These structural injection mouldings are typically made from polypropylene with steel reinforcements yet this one has been designed entirely from glass-fibre filled polyamide.
Environmental drivers …
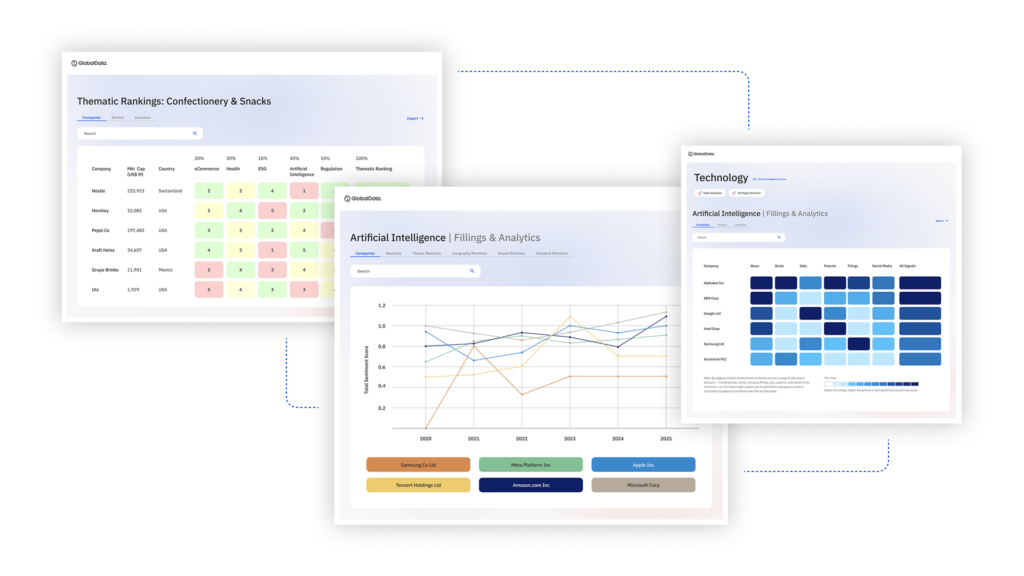
US Tariffs are shifting - will you react or anticipate?
Don’t let policy changes catch you off guard. Stay proactive with real-time data and expert analysis.
By GlobalDataThe environmental and economic requirements for reduced fuel consumption have also led to an increase in the use of lightweight materials for components that bolt on to a conventional steel vehicle, but at a cost.
…leading to more use of high strength steels…
Meanwhile, we continue to see more use of high tensile steels. The trend in the increased use of higher strength steels such as 600 and 800 MPa material and ultra-high strength steels such as boron steel is clear, as are the weight-saving benefits. The challenge for auto industry is for better collaboration of OEMs and their supply chain to exploit these materials. We will certainly see lighter all-steel vehicles, especially in the highly cost driven A, B and C segments.
Although the manufacture of body panels and various assemblies have historically formed part of the automaker’s in-house activities, these parts are increasingly being outsourced. We see a range of strategies in this field and it is difficult to see any clear trend emerging in the outsourcing of sheet metal forming. Whilst it is true that Western Europe faces a particular challenge from Eastern Europe and even further afield, rigour in quality has yet to catch up with the enthusiasm for cost reduction in many cases. However, there are now increasing opportunities for suppliers to develop modular assemblies such as doors and walk-in-front-ends. The rapid growth of die quenched (boron steel) pressings has been mainly due to tier 1 supply. Automakers prefer to press the full-finish exterior body panels in-house to reduce the potential for transport damage and control quality.
…plastics…
While the use of aluminium, magnesium and different grades of steel are all under scrutiny by automakers in a bid to optimise certain factors, the use of plastics in vehicles has significantly increased over the last decade. The trends toward the increased use of plastics in exterior and structural/functional/powertrain components have been driven by innovations in material, moulding and painting technologies, which have improved the performance and appearance of moulded plastic components as well as lowering their costs. The design freedom that plastic offers is also key to its increased use. Not only does plastic allow for the manufacture of products that cannot be manufactured with other materials, plastic makes it possible to combine several parts, saving weight and cost. Additionally, recently introduced plastics that can withstand the hot, corrosive environment of the engine compartment are becoming more prevalent.
As we understand it, an increasing proportion of both structural and non-structural components are being made from plastics rather than steel. Some of the structural components include grille opening retainers, floor panels, bumpers and support beams. Non-structural components include exterior trim panels, grilles, duct systems, tail lights, fluid reservoirs, intake manifolds, valve covers and drive train components. An auto executive gave us his observations, adding: “Structural plastic components are difficult to integrate with the rest of the structure and so at present they are generally restricted to parts that can be added after the steel structure has been completed. There are some restrictions with regard to durability and repairability if they are used in some areas of the vehicle.”
…and organic materials
Meanwhile, the use of organic materials in cars is not new. For some time, component suppliers and automakers have focused on promoting environmentally friendly technologies in all product segments. In the area of seating, for example, coconut fibre seat pads have been used in order to meet manufacturers’ economic and ecological objectives while contributing to sustainability. For example, Mercedes-Benz uses coconut matting, crushed olive stones and even sawdust in certain vehicles.
For its part, Toyota is using plastic components made from plants for its Prius. Known as ecological plastic, the plant-based foam and injection-moulded parts are found in several locations throughout the new car including the scuff plates, deck trim and seat cushions. The plant based plastics replace conventional plastics made using petrochemicals, cutting CO2 emissions over the life of the product (from manufacture to disposal) and helping to reduce petroleum use. Ecological plastic emits less CO2 during a product’s life cycle because most of the CO2 emitted at disposal was originally captured during photosynthesis while the plant was growing.
What premium will OEMs pay for weight reduction?
During the course of this research, we asked our industry contacts: what premium will OEMs pay for weight reduction? A glassmaker told us: “That’s a question that we would all like to know the answer to. We have some ideas of course but in reality that number can vary a lot from OEM to OEM and specifically from car line to car line depending on the phase of the design process they’re in. As they get closer and closer to the end, where their targets could potentially not be met then that last bit of weight is extremely precious, but if they already are meeting their target weight numbers then the weight is not such a big issue. As you know, when they start designing the car they have a target weight in mind and inevitably they’re always heavier than they want to be and then they try to get the weight out at all stages of their design process, so depending on what stage of that process they’re in the value could change.”
An independent engineering expert said: “This is a great topic: it’s much discussed and everyone seems interested in the answer. There are a number of factors that affect this answer:
-
What is the cost of alternative routes to CO2 reduction, such as powertrain improvement? This changes as technologies evolve and legislation develops.
-
What are the other benefits of weight reduction, for example increased dynamic ability? A manufacturer of high-performance cars will be much more willing to pay for weight reduction because it delivers a lot more value than CO2 reduction.
-
What are the other pressures on weight, for example additional safety systems or hybridisation, that may change the value algorithm?
-
What are the commercial implications of a little more weight on this model? Can it be offset by a new, ultra-low CO2 model about to be launched or is this the one that needs to make the difference?
-
What are the spin-out savings? In an EV, the acceptable price of weight reduction technology will be much higher because the synergistic benefits – less expensive batteries needed – create significant savings.
-
What is the publicity / brand value of the weight reduction solution? Audi helped to transform its brand by introducing aluminium BiW. I’ve seen a volume manufacturer introduce a lightweight technology with a big cheer, then quietly swap it for a conventional steel solution.
“The answer to these questions are different for each vehicle manufacturer, so the range of answers to the question is broad and shifting. There are $/kg numbers in the industry but there is so little agreement that everyone listens intently to any discussion.
“As far as trends are concerned, my impression is that there hasn’t been the upward escalation that people expected. Yes, weight saving does have a premium, but some of the technologies that were predicted have not happened because more affordable solutions – like powertrain and tyre improvements – have been implemented.”
Among those we talked to, a manufacturer a range of infotainment products purely for the automotive industry told us: “We have offered several lightweight material technologies to our customers,” said an executive. “In the main, our customers have looked for lightweight loudspeakers, as this is the biggest opportunity for weight saving.” This company is offering neodymium as opposed to ferrite for premium loudspeaker magnets. “We have offered a growing number of lightweight structures for a number of years but this has speaker technology been the primary component where customers have been prepared to pay a premium.”
During an interview with just-auto, Karl-Friedrich Stracke, President Fahrzeugtechnik & Engineering of Magna Steyr told us: “In terms of what we see on the market this depends very much on the segment of vehicles. For example, mass produced segment A, B and C cars come with a per kg amount in the range of 2-5 Euro they generate for weight reduction, whereas a premium automaker may be willing to pay more.”
Swamy Kotagiri, executive vice president and chief technology officer of Magna International told us: “There is a trade-off between powertrain investment (cost) and lightweight materials investment (cost) as enablers to meet the fuel economy and CO2 target that are being legislated for the future. As costs are generally passed on to the consumer, automakers are carefully considering the most optimised solution for their vehicle fleet.”
See also: Global vehicle lightweighting – technology, trends and the future