In his speech to the Robert Bosch 55th International Automotive Press Conference, in Boxberg, Günther Plapp, Executive Vice President Development, ABS and Brakes Division of Robert Bosch GmbH, reviewed recent developments in electronic brake control systems. ‘Brake-by-wire’, using the electro-hydraulic brake (EHB) will be ready for series production soon and promises to raise braking comfort. Mr Plapp’s speech is reproduced here.
In 1999, 4,600 persons died in traffic accidents in Germany. This number represents a reduction of more than 50 percent over the last 30 years, even though during that same time period driving miles has increased significantly. The trend is encouraging, but the number is still alarmingly high. Bosch has made significant contributions to this reduction and together with automobile manufacturers has developed products with the goal of improving passive and active safety of motor vehicles. Good examples are airbag and anti-lock brake systems, which have become standard equipment in most new cars.
ESP is recommended for series applications
Two years ago, the Institute for Vehicle Safety in the Association of German Insurance Businesses e.V. (GDV) analyzed the causes of accidents with serious or fatal injuries. From a total number of 15,000 reports, the experts evaluated 831 accidents in depth. The analysis revealed that 60 percent of all accidents with fatalities were caused by side-impact crashes. In 30 to 40 percent of all fatal accidents, the vehicle began to skid due to excessive speed, exaggerated steering reaction or driving error. Based on this result, the Institute issued a clear recommendation in favor of safety systems, such as the electronic stability program (ESP), which enhances vehicle stability. ESP can prevent skidding or at least better control the vehicle. According to experts, introducing ESP as standard equipment could reduce the number of serious accidents.
Such analyses and recommendations indicate how important it is to continue previous developments in the area of vehicle stabilization. The objective is to achieve more wide-spread use of low-cost driving stability systems in all passenger vehicle classes.
A skidding vehicle can be stabilized by specific braking of individual wheels, by reducing the engine torque and making steering corrections. Techniques to influence the brake system automatically or to automatically reduce torque have been in use for some time, but systems with automatic steering intervention are still in the development phase. Anti-lock braking systems (ABS) and traction control (ASR) have already improved vehicle safety in a significant way. ESP offers the conscientious driver safety technology, which controls the vehicle in almost every driving situation. This safety can be augmented even more with the brake assistant. Its function is relatively simple and can be integrated into the ESP control unit without any extra components.
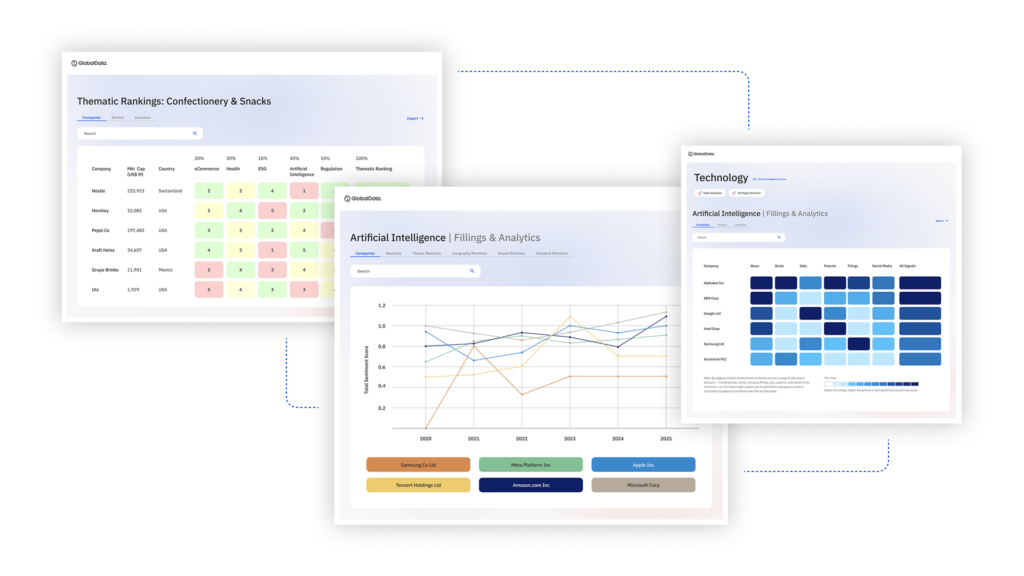
US Tariffs are shifting - will you react or anticipate?
Don’t let policy changes catch you off guard. Stay proactive with real-time data and expert analysis.
By GlobalDataESP is comprised of a hydraulic modulator and a control unit with sensors, which determine and evaluate the driving situation. ESP hydraulics quickly build brake pressure on a single wheel in critical situations in order to counteract the undesired skidding motion. This pressure increase occurs automatically on the wheel, without driver involvement. The brake impulse can thereby stabilize the vehicle at all times and return it to the proper course. The system may also reduce the engine torque, which provides an added stabilization effect.
![]() |
Bosch have produced over 50 million ABS sytems |
The benefits of ESP for the driver include:
- Improved steerability in critical situations,
- Reduced danger of slipping or skidding,
- Greater vehicle stability within physical limits, and
- Optimized stopping distances.
ESP therefore makes an important contribution to preventing serious accidents.
X-by-wire-systems replace purely mechanical systems
A general trend is seen in the further development of systems for fully-automated vehicle guidance and steering, or in other words, mechanical systems are being replaced with “X by Wire” systems. These systems determine the driver’s commands via sensors, process the information electronically and pass on derived steering commands to the actuators. A current system is “Drive by Wire”, the electronic gas pedal.
Bosch is also working intensively on electronic systems in the areas of braking and steering. “Steer by Wire” and “Brake by Wire” are prerequisites for new safety and comfort enhancing functions, which can only be created by the interaction of several vehicle systems.
Brake-by-wire separates the mechanical hydraulic connection between brake pedal and wheel brake. Sensors determine the driver’s braking command and transmit this information to an electronic control unit. Using the corresponding actuators, the control unit creates the required brake effect on the wheels.
At the moment, the best concept for brake-by-wire is the electro-hydraulic brake, or EHB. The system uses proven hydraulic brake components and will soon be ready for series production. Bosch is developing the EHB together with DaimlerChrysler and will start series production for the first time this year.
![]() |
mechanical systems are being replaced with “X by Wire” systems |
For conventional brake systems, the driver creates brake pressure in the wheels via the master brake cylinder or stabilizing intervention is ESP. In contrast, EHB provides the brakes with a brake fluid supply from the hydraulic high-pressure reservoir, which is sufficient for several braking events. A piston pump driven by an electric motor supplies a controlled brake fluid pressure between 140 and 160 bar in the gas diaphragm reservoir.
When the brake is activated or when ESP intervenes to stabilize the vehicle, the EHB control unit calculates the desired target brake pressures on the individual wheels using its software algorithm. Because it determines the necessary braking pressure for each of the four wheels separately and also measures them individually, it can regulate the brake pressure on the individual wheels via the wheel pressure modulators. These four pressure modulators consist of one inlet and one outlet valve, controlled by electronic output stages.
The interface with the driver is the brake actuation unit. By way of a distance sensor and a pressure sensor it measures on the master brake cylinder how fast and how strong the brake is actuated. The control unit processes this information and generates the control signals for the wheel pressure modulators. Normally, the master brake cylinder is detached from the brake circuit. A pedal travel simulator creates normal pedal feedback. If ESP intervenes, the high pressure reservoir supplies the required brake pressure quickly and precisely to the wheel brakes, without driver involvement.
EHB raises braking comfort
The crucial performance feature of the electro-hydraulic brake, or EHB, is that it raises braking comfort. Because the brake pressure can be regulated in a completely variable way without driver actuation, vehicle guidance functions such as Adaptive Cruise Control (ACC) can be designed in a very comfortable way.
Due to the low actuation forces of the brake pedal, the driver can easily raise the braking force up to a full ABS stop with the help of EHB.
Even with ESP intervention, vehicle stabilization is more comfortable with a fast and precise adjustment of the desired wheel pressures. The vehicle controller intervenes earlier and stabilizes the vehicle in a way almost undetected by the driver. So that the driver recognizes a critical situation, ESP intervention also can be signaled optically.
Additional advantages of EHB are listed below:
The soft-stop-function provides a soft and smooth stop. What is frequently referred to as “chauffeur braking” is now provided by the electro-hydraulic brake.
Reduces skidding in curves by means of automatic braking intervention
- The dry brake function of EHB carries out regular short and weak brake impulses on wet roads, in order to dislodge the water film on the brake disks and to assure the full and immediate brake effect every time. Switching on the windshield wiper activates this function.
- A traffic assistant brakes the vehicle with pre-defined deceleration when the driver removes his foot from the accelerator pedal. He doesn’t have to constantly change back and forth between pedals.
- The drive away assistant prevents rolling backward on a hill and simplifies the drive away process. The function is activated when the car is standing, by quickly and firmly pressing down the brake pedal. The brake effect is automatically canceled the next time pressure is applied to the accelerator pedal.
- ACC Stop & Go is an upgrade of the ACC-function for stop-and-go traffic or city driving. In conjunction with other sensors, EHB brakes the vehicle to a standstill while the distance to the vehicle ahead is always considered. If the driver ahead accelerates, the car drives away automatically and follows.
Consequently, EHB provides the prerequisites for a number of comfort functions tailored to the driver. The automaker therefore has additional ways to distinguish himself from the competition.
In parallel to EHB, the electro-mechanical brake, or EMB, is also being discussed. But introduction as a full-value brake system will take some time. A significant problem is the task of developing a low-cost and light wheel brake, which fits into the tight interior space of the rim. In addition, EMB also requires a high-grade and sophisticated 42-volt power supply.
In contrast, EHB does not have any additional space requirements near the wheel brake and does not add any extra weight. To save energy, a well-designed 14-volt power supply is adequate. Availability in an emergency situation is assured by direct hydraulic intervention from the master brake cylinder to the front axle brakes. Because of these advantages Bosch expects that EHB will take over the market quickly. With production launch in 2001, Bosch is setting another milestone in active driving safety.
By 2005, EHB will only be available in the upper mid-sized and luxury classes of automakers and will therefore be able to show its advantages on a small scale only. Lower-cost EHB systems will make this technology available for other vehicle classes as well. Market developments of EHB could be comparable to that of ESP. Since the start of series production in 1995, Bosch and its competitors already have high equipment levels in some markets and the trend is rising.
EHB is another important step in the overall network of automotive safety systems. This electronic brake system has created an important prerequisite for automatic vehicle guidance.
Günther Plapp, Executive Vice President Development, ABS and Brakes Division of Robert Bosch GmbH
|
Esp Penetration Rate |
![]() |
EHB Diagram |
![]() |
To view related research reports, please follow the links below:- X-by-Wire – How electronics will reinvent the motorcar |