February 2002 sees the production of the last vehicle at the Dagenham Estate, as the 473 acre site prepares to become home to Ford’s global centre of excellence for diesel engine design and manufacture, Dagenham Stamping Operations, and to CEME, the Centre for Engineering and Manufacturing Excellence.

Once Ford’s biggest and older UK car plant, Dagenham built such famous names as the Anglia, Prefect Zephyr and Cortina over 71 years and 11 million units. Although Ford will say otherwise, officially, public outcry was so loud when plans to close Dagenham were outlined in May 2000, the factory was given far greater prominence as a centre of diesel engine production for the entire Ford group, in a £340 million investment programme, than originally planned.
Additional community-sweetening comes in the form of a multi-million pound “centre for engineering excellence” which has been described as as the UK’s first “seamless” university. Funded by a Ford-public sector partnership, the centre will train apprentices, carry out post-graduate research and offer business management training. Just like the car factory used to.
Canning Dagenham car assembly means Ford is axing about 1,100 workers, the latest in a long line of departees from a site often troubled by industrial action over the decades. Diesel engine building will require an extra 500 staff with the net transfer rate put by one source at around 250.
End of an era
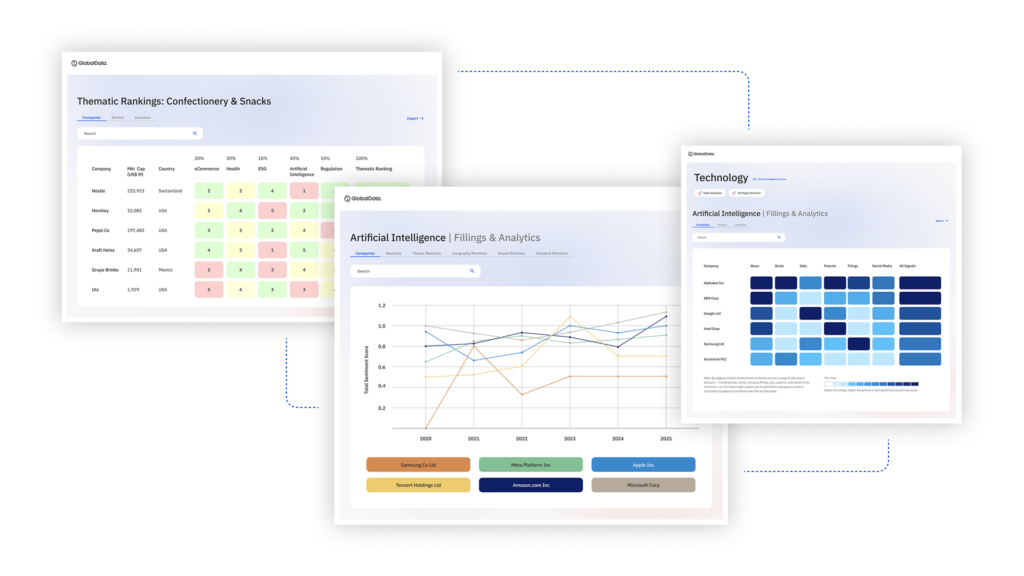
US Tariffs are shifting - will you react or anticipate?
Don’t let policy changes catch you off guard. Stay proactive with real-time data and expert analysis.
By GlobalDataThe new role for the site comes at the end of an era which has seen the production of some of the most famous Ford vehicles including; the Prefect, Popular, Consul, Zodiac, Zephyr, Consul, Anglia, Cortina, Granada, Sierra, and Fiesta. By the time the last car rolls off the line in February 2002, Dagenham will have assembled 10,980,368 vehicles.
The story of Ford at Dagenham however, really begins in Manchester, where the first Ford factory in Great Britain was a converted carriage works at Trafford Park. Opened in October 1911, the Trafford Park factory was originally intended to only be an assembly plant, but over the years an increasing number of manufacturing operations were undertaken until eventually the vehicles were British made.
The first car produced was the Model T, which had been launched in Britain as an import in 1909. After the First World War, as demand grew, it became clear that there was a need for a new factory specially designed for large scale production. Manchester was, after all, a largely improvised enterprise that had outgrown itself.
Building on marshes
In 1923, Edward Grace, the Manager of Henry Ford and Son of Cork, was sent to England to find a suitable site. His brief was to find a location where a miniature of Ford’s main US plant could be created to serve the European markets. The final choice of Dagenham came as a surprise to many people.
The original 310-acre site was bought in 1924 for £167,695, and was said by some experts to be unworkable. It certainly presented a considerable challenge to the construction engineers, but once it was agreed that the difficulties were surmountable, the geographical advantage of the site proved decisive.
A Thames-side factory was desirable in that it gave a quick and easy outlet to European ports as well as good access for raw materials. The London County Council was building a vast new housing estate nearby, so a supply of labour would be readily available and the nature of the surrounding area allowed for future expansion.
In the evening papers of July 10, 1924, plans were announced for a factory that could build 500 cars per day, approximately three times the output of Trafford Park. The site at Dagenham, a low water-soaked tract, still looked highly unpromising when Henry Ford’s son Edsel cut out the first sod of earth on the site with a silver spade on May 17, 1929. The public however had already expressed its confidence in the entire venture by heavily over-subscribing for the shares.
Early in 1930, Ford purchased an additional 191 acres at Dagenham bringing the total site area to 501 acres. Two years later the factory, built on 22,000 concrete piles that had been driven 80 feet into the marshland, was complete. It had its own blast furnace, foundry, jetty and power station.
The key to the decision to purchase the site had been the potential of the River Thames – and the jetty was soon berthing vessels of up to 10,500 tonnes ready to link the plant directly with the world’s seaways.
Within a few days of the last car rolling off the production line at Trafford Park, the new Dagenham complex came to life.
Production begins
Special trains carried 2,000 employees with their families and possessions to Dagenham from Trafford Park and many more people were engaged from local sources and elsewhere. At 1.16 pm on October 1st, 1931 the first vehicle to be build at the new Dagenham plant left the production line. It was a model AA truck, number AA 479001, destined for Ford dealers Quicks of Manchester and driven off the line by A R (later Sir Rowland) Smith, Ford’s General Manager.
Built at a cost of some £5 million, the Dagenham factory had opened in the depths of the depression. Business was so bad that in the last three months of 1931, Ford sold only five cars – though production of trucks was, fortunately, brisker. At the time the press referred to Dagenham as a “magnificent gesture of faith in Britain’s commercial future … a lighthouse of hope in a storm-tossed sea of industry.”
Right from the early days, the Ford-pioneered principles of mass production were applied and in its first full year, Dagenham produced 22,595 cars and trucks. As the depression lifted so the number of vehicles produced increased and in 1933 6,900 employees built 36,424 cars, plus an additional 14,318 trucks and tractors.
The main models produced at Dagenham up to the outbreak of the Second World War were the 8 hp Model, the 10 hp Model C and 22 hp and 30 hp V8 ranges. The Ford Model Y has the distinction of being the lowest-priced, fully-equipped saloon car ever to be made by any manufacturer. The “Popular” model, introduced in 1935, was the first car to be offered at just £100.
The war years
From 1939 it was all hands to the war effort. And during the next six years the plant produced 360,000 light vans, army trucks, balloon winches, mobile canteens and Ford V8-powered Bren Gun carriers – plus 34,000 Merlin aero engines.
Dagenham’s famous Fordsons also accounted for 95 per cent of Britain’s vitally important tractor production during the war.
Post war production
At the end of the Second World War, British Ford manufacturing facilities stood virtually as they had been in 1931, but pent-up demand at home and abroad now created a tremendous opportunity for expansion.
The Kelsey Hayes Wheel Company was acquired (now part of the Body Plant), an extension was built onto the existing factory to boost tractor production and in 1953 Briggs Motor Bodies were also acquired – the company that had been supplying Ford bodies since the 1930’s.
In its product range, too, the company now made up for time lost during the war years. At the 1950 Motor Show the revolutionary new Consul and Zephyr range of cars were shown, the first Ford cars to employ completely integral body/chassis construction.
A £75 million expansion and modernisation programme was launched in 1954, all of which was financed from the company’s resources. Completed in 1959, it increased floor space by 50 per cent and doubled production capacity from 233,624 cars, truck and tractors in 1953 to 459,405 cars, trucks and tractors in 1959.
The biggest projects at Dagenham in this phase of expansion were a completely new foundry costing £7.5 million and opened in 1957, a new £11.5 million Paint, Trim and Assembly Building which took over the final output of all cars from 1959, a blast furnace to replace the one that had operated virtually non-stop for nearly 30 years and a new press shop to increase the capacity and efficiency of the Body Plant.
Until the 1960s, virtually all the company’s cars, commercial vehicles and tractors were produced at Dagenham with an increasing number of components being supplied from subsidiary plants, but by the middle of the decade a new pattern of production had emerged. Car and light van production was shared between Dagenham and the £30 million factory at Halewood on Merseyside; tractors were built at Basildon, Essex; trucks and medium vans were made at Southampton and Langley (Berkshire).
The next major new car produced at Dagenham – and destined to become one of the country’s favourites, was the Ford Cortina. By the time the last Cortina MkIV left the line in 1981, the plant had built over three million – and the total production of the vehicle stood at over 4 million.
By this time, Dagenham was already producing the Ford Fiesta, introduced in 1976, and the Ford Sierra started production in 1982.
New metal stamping and over 100 body construction robots were introduced for the first time for the Sierra range, introduced in 1982 meant expenditure of £210 million, while new equipment for the manufacturing of the 1.6 diesel engine fitted to Escorts, Fiestas, Orions and Escort vans cost £220 million.
The 1.6 diesel engine was replaced in 1990 by the 1.8 litre version, for which Dagenham Engine Plant is Ford’s sole European source, as it is for all Ford diesel engines including the 2.5 direct-injection diesel engine fitted to its light and medium commercial vehicles.
In 1982/3, new fully automated paint systems were brought into commission as the result of an investment of £40 million, while at around the same time, the Thames Foundry closed in 1984, and the Forge in 1986.
1985 saw the announcement by the company of its intention to provide new facilities for the production of an advanced 2.0 Litre DOHC petrol engine at a cost of £157 million. These engines were finally introduced in 1989.
In 1990, Dagenham became a single car-line plant. Sierra production was transferred to Ford’s factory at Genk, Belgium leaving Dagenham to concentrate on the manufacture of the new Fiesta range of cars and vans. At the same time, the Fiesta range was expanded by the inclusion of the high roof van – the Courier.
In its first full year as a single-car-line plant, Dagenham built a total of 227,378 vehicles – at that time, the largest number since 1972. Since then, the highest daily production record was set on January 14, 1998 when 1,357 vehicles were produced.
The two-millionth Dagenham-built Fiesta, a red Fiesta 1.1. Azura was produced in June, 1995, and was donated to the local community to raise funds for local charities. January 1996 is also a date worth recording, when Dagenham launched production of an additional model – the Mazda 121. In its launch year, 24,528 Mazda 121 models were produced alongside 223,388 Fiesta cars, vans and Couriers.
Further developments in the mid 1990’s included investment in the Single Final Line in the Assembly Plant, costing £14 million and in the late 90’s a new £20 million Dip Phosphate facility.
In October 1999, the London Development Agency purchased 98 acres of land on the Dagenham estate (the Old Foundry site and Mudlands sites) to create a supplier park for local industry.
Dagenham’s diesel future
May 2000 saw Ford announce the ending of vehicle assembly at Dagenham as part of its European Restructuring. A new role for the Dagenham Estate was set out, with the development and expansion of the Dagenham Engine Plant to become Ford’s primary centre for the engineering and manufacture of Diesel Engines. Over a five-year period, Ford’s investment in the Dagenham Estate will total $600 million.
At the centre of Ford’s plans to create a world-class, high technology, diesel engineering and manufacturing centre at Dagenham is the new Clean Room Assembly Hall, the first major new building to be constructed at Dagenham for more than 30 years. The Clean Room will be one of the most modern manufacturing facilities in Europe and will significantly boost diesel engine production capacity at Dagenham from today’s level of around 650,000 units per annum to up to 900,000 engines by 2004.
Together with the increased output of petrol engines at Ford’s Bridgend engine plant, plans for which were announced in February this year, the UK will be producing around two million Ford engines per year by 2004 – that means that one in four of the vehicles that Ford sells around the world each year will be powered by an engine built in the UK.
Other operations
Since the restructuring announcement in May 2000, $36 million has been spent in upgrading Dagenham Stamping Operations. The operation provides vehicle panels, sub assemblies and wheels to Ford plants throughout Europe and emerging markets. Other activities on site include: vehicle storage, movement and transport operations, group tooling, knockdown operations, a powerhouse and various services.
CEME
In October 2001, building work started at Dagenham, on land donated by Ford to build the Centre of Excellence for Manufacturing and Engineering (CEME). CEME is a unique partnership between Ford, the London Development Agency, Barking and Havering FE colleges and the Universities of Loughborough and Warwick.
The Centre will support education and skill training for the local area, to provide a seamless route from basic skills to higher education and research programmes around manufacturing, engineering, commercial and technological themes.