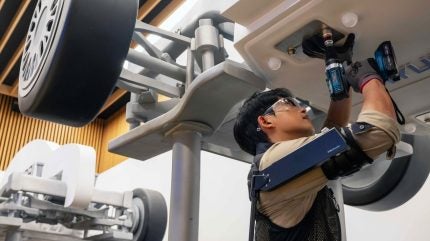
Various technologies are shaping the future of work in the automotive industry, transforming how vehicles are sold, maintained, designed, and manufactured. The future of work will reshape both factories and offices, encouraging greater collaboration between humans and technology and empowering workers with new digital skills.
Automakers worldwide are generally quick to adopt new technologies to maximize efficiency in their operations and are already incorporating innovative new methods in vehicle design, manufacturing, and sales. They aim to redefine working relationships within the sector.
Future of Work in Automotive – Strategic Intelligence
Hyundai and Kia are introducing wearable robots
In November 2024, Hyundai Motor and Kia Robotics unveiled an industrial wearable robot called the X-ble Shoulder. The exoskeleton aims to increase worker efficiency while reducing musculoskeletal injuries. Although robotics has a long history within automotive production thanks to its efficiency, precision, and ability to perform repetitive tasks, human workers are still needed for complex decision-making, delicate tasks, and maintenance. However, using exoskeletons like the X-ble Shoulder will help lower the number of work-related injuries that arise from industrial tasks, ultimately reducing costs and improving worker well-being.
The device is unique because it generates assistive force through its muscle compensation module instead of an electric system, using a non-powered torque generation. This feature allows the robot to be used without a battery, making it more convenient to maintain. The device’s carbon composite material makes it lightweight, enabling workers to work long hours without difficulty.
In jobs that require repetitive motions, such as assembly work or operating machinery, repetitive strain injuries are extremely common, often affecting the shoulders, hands, and wrists. The introduction of devices such as the X-ble Shoulder represents a practical approach to improving worker health and safety, as seen by its ability to reduce up to 60% of shoulder load.
The device should be ready for commercial distribution in the first half of 2025. Exoskeletons are the fastest-growing sub-segment of robotics, according to GlobalData research, and are forecasted to grow at a 34% cumulative average growth rate (CAGR) between 2023 and 2030.
Toyota’s concept car with 3D-printed parts
In July 2024, Toyota unveiled its Hyper-F concept car, a high-performance sport utility vehicle (SUV) that incorporates 3D-printed components and advanced materials. Developed by Toyota Customizing and Development Asia (TCD Asia) and based on the Toyota Fortuner platform, the vehicle showcases Toyota’s use of 3D printing technology.
The Hyper-F concept car features 3D printed components produced from plastic granulation, implementing technology from Mitsui Chemicals. This manufacturing process enables the creation of cost-effective and stable large-format parts. Notable applications include 3D-printed panels for the hood air ducts and the use of Tafnex on the front bumper. Tafnex is lightweight, strong, and moldable. It helps reduce the vehicle’s weight and enhance its performance. These advancements in manufacturing processes aim to decrease development times and investment costs, making high-performance enhancements more accessible and efficient.
The Hyper-F concept car underscores Toyota’s commitment to integrating advanced manufacturing techniques into automotive design. The Hyper-F’s success could pave the way for broader adoption of 3D printing technologies in mass vehicle production and rapid prototyping.