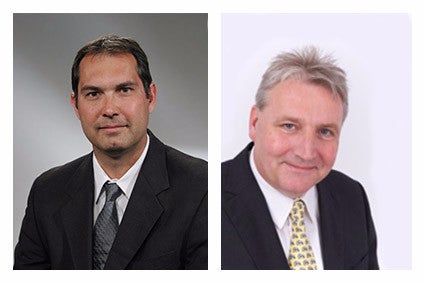
Dow Automotive Systems, part of The Dow Chemical Company, has been in the business of adhesives for decades. Dr Matthew Beecham spoke to Dr Andreas Lutz, head of adhesives R&D with Dow Automotive in Horgen, Switzerland and Dr Stefan Dehnicke, R&D leader Specialty Adhesives at Dow Automotive in Schwalbach, Germany about the challenges of joining certain lightweight composites and recycled parts.
Could you tell us a little about Dow’s automotive adhesives and the messages that you put out at the recent JEC show?
Dr Andreas Lutz: The main messages during JEC and bonding of composites concern a couple of aspects. First is that adhesive joining provides the best joint performance with regard to durability and energy absorption. Further, our adhesives result in an excellent adhesion without using surface treatment thereby eliminating an expensive process step. More general benefits include improved car body performance with regard to stiffness and crash management, and enabling of a material mix including CFK to realise lightweight targets.
What are the challenges with joining certain lightweight composites?
Dr Andreas Lutz: Lightweight composites can be joined effectively thermally and mechanically. In comparison to mechanical joints the adhesive technology provides the advantage of maintaining the maximum reinforced composite material performance by not damaging the composite structure when drilling holes for the mechanical fixations. If passing an oven the different CLTEs (Coefficient of Linear Thermal Expansion) of the different materials need to be addressed like with tailored adhesives and specific engineering solutions. But if you bond CFRP to CFRP then there are no differential expansion issues.
Another challenge of adhesive technology is that it needs a broad adhesion spectrum on different surfaces such as KTL (e-coat), different composites or coated metals. Also, forming durable joints requires the development of specific adhesive solutions. Thus, to achieve an optimum in bonding composites, any supplier needs to have a deep understanding of surface technology and the ability to supply tailor made solutions while maintaining cost-efficiency and easy to integrate into their processes. Standard adhesives will not be successful.
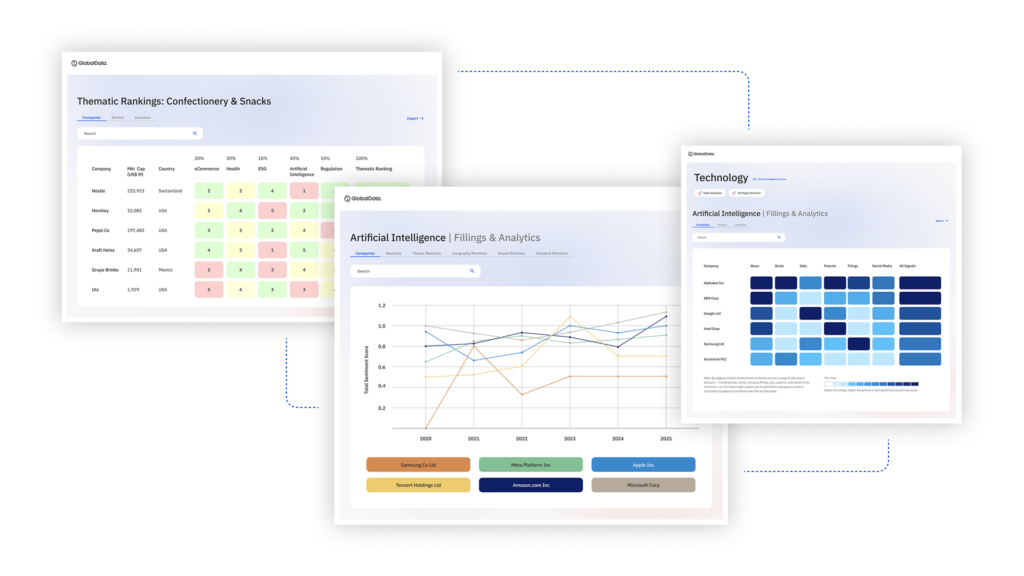
US Tariffs are shifting - will you react or anticipate?
Don’t let policy changes catch you off guard. Stay proactive with real-time data and expert analysis.
By GlobalDataFor under-the-hood applications, I guess adhesives face challenges on not just higher temperatures but joining a number of different materials and recycled parts.
Dr. Stefan Dehnicke: Dow Automotive Systems offers a broad range of different epoxy and PU based adhesives as well as rubber-to-metal bonding solutions and UTH application area where a wide range of different rubber types are bonded to metal. The challenge in UTH is to develop adhesives that can stand glass transition temperatures above operating temperature to achieve a durable joint. Further, solutions need to be heat, glycol and water resistant. Cooling agents for example.do represent a specific challenge due to their additives that attack the bond. Also, hot glycol is an aggressive element that attacks metal rubber composites. Recent solutions from Dow Automotive are overcoming these challenges and are in continuous development to catch up with the developments with cooling solutions and glycol behaviour.
In terms of bonding windscreens to the car frame, what are the safety issues there?
The remainder of this interview is available on just-auto’s Global light vehicle materials market- forecasts to 2030