IFR Automotive has developed and patented its Twin Brake Disc (TBD) system. As the name implies the lightweight stainless steel brake system comprises twin discs, each with turbine shaped slots for maximum air cooling and braking efficiency. To find out more, Matthew Beecham talked with Ignacio Fernandez of IFR Automotive.
The principal characteristic of this design is that heat is dissipated quickly and does not accumulate, thereby permitting much thinner discs. The result is a significant weight saving of more than 70% compared with normal brake systems.
Having more than one brake disc also makes the calliper requirements smaller, and hence much lighter, further reducing the total mass of the brakes, which in turn helps to reduce the overall weight of the vehicle.
In addition, a lower unsprung mass is immensely beneficial for a vehicle’s ride and handling performance.
The claimed advantages of this system are:
- maximum air cooling and braking efficiency;
- improved active safety from improved handling of the vehicle;
- more traction from increased contact of the wheel with the road;
- improved ride comfort;
- less fuel consumption and fewer emissions through ultra lightweight design;
- better feel of the brakes for the driver by avoiding the need for a servo;
- increased durability of brake pads and discs.
On the company’s Aspid technology demonstrator vehicle, the company claims that the combination of the TBD brake system and patented DLR wishbone suspension, results in a very low unsprung mass which matches that of an F1 car built in composite materials – yet on the Aspid this has been achieved with steel brake discs and an aluminium suspension. Compared with normal road car brake systems, the weight saving is more than 70%.
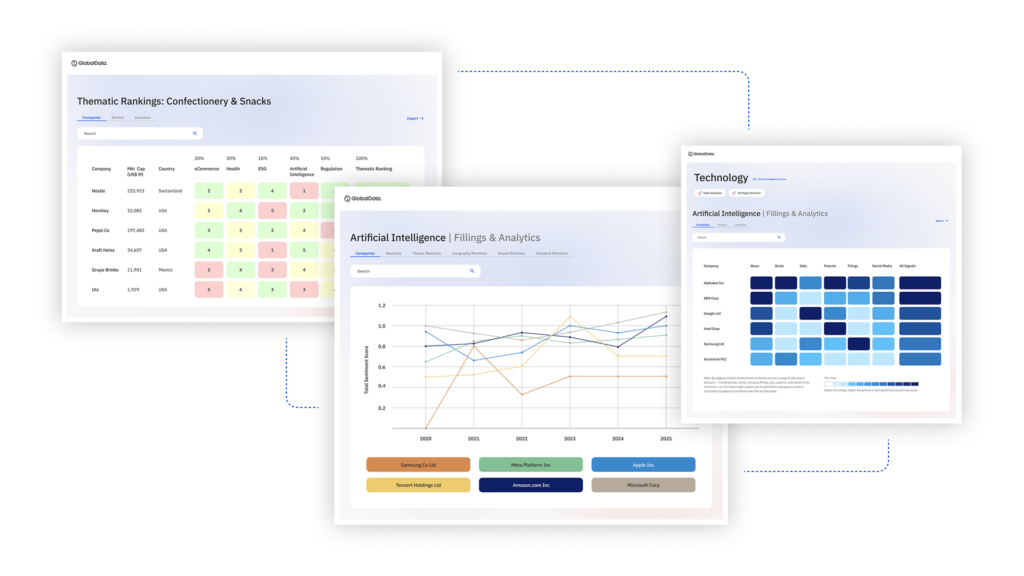
US Tariffs are shifting - will you react or anticipate?
Don’t let policy changes catch you off guard. Stay proactive with real-time data and expert analysis.
By GlobalDataj-a: What are the forces driving innovation in foundation braking for passenger cars and light trucks? Are those drivers the same for every car segment?
Ignacio Fernandez: In terms of further development, the major challenge is about reducing the weight of the system, which is probably the most crucial factor for two main reasons. The first relates to the unsprung mass of the vehicle, which has a significant impact on the forces transmitted to the chassis, which are proportional to the unsprung mass. Consequently, the unsprung mass of the brakes has a big impact on the set-up of the suspension and the vehicle dynamics generally, influencing both active safety and ride comfort.
The second crucial factor is that the unsprung mass is also rotating and has inertia, which also has to be managed. For IFR Automotive, which is focused on lightweight technology, the main driver behind our technical innovations is weight reduction. Whether a disc or drum, it’s a very heavy component located in the most critical part of the vehicle. As well as providing the fundamental active safety and vehicle dynamic benefits of lightweight brakes, IFR’s advanced twin-disc system, or TBD, also provides a significant step change improvement in resistance to fading at medium and high speed, comparable to that achieved when the industry changed from drum to disc brakes. The improved fade resistance compared with a conventional disc system is one of the major benefits resulting from the rapid cooling delivered by IFR’s twin-disc brake system.
j-a: To what extent do those drivers change when looking at the developing regions, such as India? For reasons of low cost and ease of maintenance, I guess the developing regions still use drum brakes. Is that correct?
IF: Today, there’s little to choose between the cost of material and the ease of maintenance. Disc systems have fewer parts to assemble, so there is less labour involved. So I think it’s less an issue of vehicle cost and more to do with the consistent performance of disc brakes. At IFR Automotive we are 100%-focused on developing a new concept for disc brake systems.
j-a: I guess reducing stopping distances and weight reduction will always be a priority when it comes to design and development of braking systems, yet to what extent is improving the brake feel important? Does it depend on the segment? Could you draw on an example where you have made some improvements in that area?
IF: Again it’s an issue of weight reduction – but even more so for hybrids and electric vehicles. Currently, when cars are driven by electric motors there is none of the engine braking that comes with an internal combustion engine when the driver lifts off the throttle. In addition, there is often a significant increase in the mass of the vehicle due to the weight of the batteries. In this case the requirements for the brakes are even bigger than for internal combustion engine cars. The heat dissipation required will be bigger, and that’s why a number of manufacturers have asked us to look into this problem.
j-a: As far as trucks and buses are concerned, high frequency brake squeals are commonplace. Could you draw on an example where you have made some improvements in that area? i.e. how did you achieve it and what were the issues (materials and construction) involved?
IF: For saloon cars the TDB system already offers clear benefits. We are now developing the technology for heavy goods vehicles, where we have to adapt the design of the disc for relatively lower speeds and heavy loads. However, we have an excellent starting point when we can dissipate 210 degrees in 100 metres from a truck travelling at 60km/h.
j-a: In what ways has the growing use of electronic control affected braking hardware?
IF: Clearly, in terms of the hardware, electronic modules do have some impact on the brake callipers. The use of stability control and traction control actuation can have also some effect on the brakes in terms of heat generation that needs some design consideration during the validation process. The most important changes however are being driven by the development of electric/hybrid cars, where there is more weight in the vehicle due to the batteries and when the car is running in electric mode the majority of the systems are not regenerating as much braking force as would be achieved with an internal combustion engine.
In the premium vehicle segment this is a particular issue for which the TBD system is proving to be an excellent solution due to its heat dissipation capabilities.
j-a: In what ways have carbon-ceramic brakes advanced over the past few years?
IF: We have been testing some carbon-ceramic brakes on the latest high-performance cars and the major problem is still there; you have to warm up the brakes before you get the right friction between the pad and discs every time you are going to brake. To me this characteristic of carbon-ceramic brakes is totally unacceptable. At IFR, we are convinced that a steel twin-disk brake system, such as TBD, provides superior performance with better cost-efficiency.
j-a: In terms of brake disc materials, in what ways has these materials advanced over the past five years? Due to economics, I guess cast iron will remain the material of choice for the foreseeable future?
IF: For mass production, at present this would seem to be the material of choice for the manufacturers.
j-a: Or could we see alternative materials being used in volume applications?
IF: It is possible some material changes may happen, but I see more radical potential developments based on changes to the fundamental concept of the brake system – such as smaller, lighter, better heat dissipation and more efficient twin-disc systems.