The apparently simple issue of braking continues to be a major focus of R&D for engineers. Here, Matthew Beecham talked with TMD Friction’s senior vice president of R&D, Andrew Dilnot about trends in the brake friction market, its newly-formed venture with Hella and the increasing use of aluminium brake disc on mass market cars.
What are the forces driving innovation in brake friction materials for passenger cars? And are those drivers the same for every car segment?
There are three main driving forces that drive innovation: the environment, cost and quality. Generally these hold for each car segment.
With regard to environmental protection driving CO2 reduction is an important aspect. Switching to lightweight vehicle components thus is a general trend. Each component supplier is challenged to contribute to an overall weight reduction. Owing to the complexity of the brake system it is not possible to change one part and leave another part unchanged for reasons of the NVH [noise, vibration and harshness] phenomena. Good NVH performance thus requires a seamless interplay of each component used in the brake system. Therefore innovation is a vital aspect in keeping pace with these developments. TMD Friction for example has developed the Q-Pad (quiet pad) that can be used with weight reduced brake systems to match customers’ quality expectations.
The phenomenon of brake drag is another point under scrutiny. Reducing the naturally occurring brake drag equally contributes to lowering CO2 emissions, as the engine has to work against less resistance.
However, environmental considerations already start when searching for the right materials being used in friction formulations. Only recently, TMD was the first brake friction manufacturer that was granted a homologation for a copper free series application for a high performance vehicle, eliminating copper in the friction formulation.
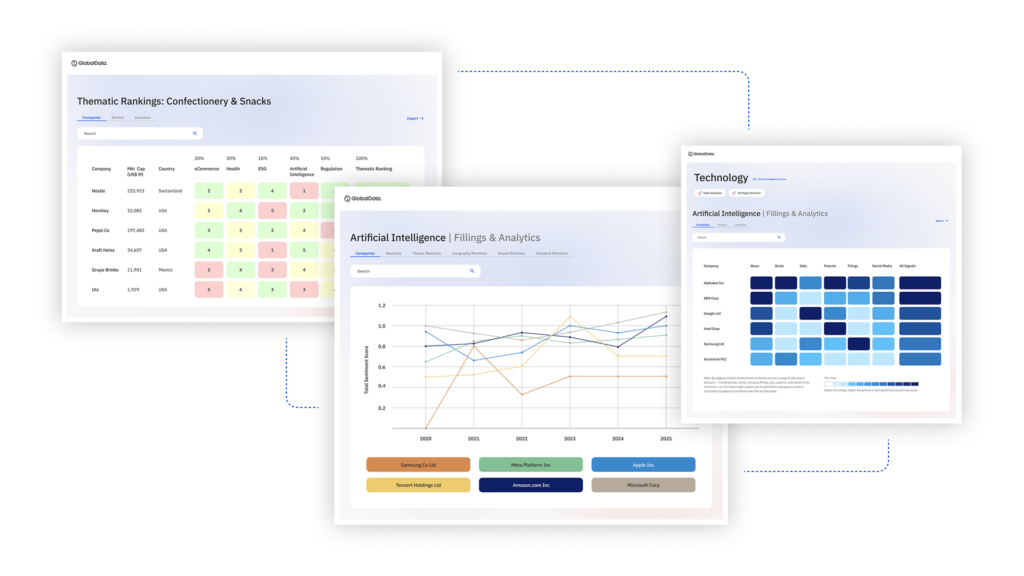
US Tariffs are shifting - will you react or anticipate?
Don’t let policy changes catch you off guard. Stay proactive with real-time data and expert analysis.
By GlobalDataAlso driven by considerations for the environment, manufacturing technology is under constant development in terms of energy consumption, scrap rate and quality assurance. TMD is increasingly using innovative production processes across different sites. These are developed at TMD and help reduce the overall energy consumption and increase quality whilst minimizing scrap rates.
Cost pressure is another important factor in driving innovation. In terms of our business we are looking at different friction formulations to influence raw material costs. But also aforementioned manufacturing processes are partially affecting costs positively though driving down costs is not their primary objective.
Last but not least quality is paramount in developing friction materials. Therefore, whatever we do in terms of the environment and cost structure, quality needs to be delivered on a “right first time” principle. Customer satisfaction is key for our business and any innovation is measured against this expectation.
To what extent do those drivers change when looking at the developing regions, such as India?
The main drivers here are slightly different. The priorities are low cost, simplicity and high quality.
In what ways does a brake pad for a hybrid or electric vehicle differ from one for a car with an ICE? And is there more of a need to reduce brake sequel on hybrid and electric vehicles?
These bring their own challenges due to the fact that the foundation brakes are not in operation all the time. So they must be more corrosion resistant and the friction material must not ‘go to sleep’ due to under utilisation. Also low drag brakes are important to increase vehicle range and not ‘waste’ energy. Low noise is a priority, EVs run at only 40db, standard cars run at over 70db.
How is your venture with Hella (Hella Pagid) shaping up?
Following some delays in securing all of the required anti-trust competition authority approvals the official start of our joint venture with Hella was postponed to the beginning of May 2013. On May 2nd the new company Hella Pagid GmbH started its business.
It is very difficult when faced with unexpected and unmanageable delays, which have no qualified timetable for resolution, to make a new business start, when this start involves the setting up and communication of thousands of new parts and the transfer of running business the difficulties are significantly magnified. Despite these issues driving some months of delay, the combined TMD/Hella project team really made a fantastic job of getting this business up and running and in finding creative and innovative ways to manage complications and difficulties arising and in preparing the business foundation for handover to the joint venture team once the new business had been inaugurated. Now our joint venture is fully operational and in spite of the initial challenges and difficulties running fully to our expectations. We have a dynamic and energetic team in Hella Pagid GmbH, and we are absolutely confident they will achieve the goals and objectives set for 2013 and beyond.
The initial premise of our JV concept with Hella was to match up the engineering strengths, product quality and brand value of TMD and Pagid, to the sales, marketing and distribution power of the Hella global aftermarket organisation. In this respect our ambitions were fully realised, we are extremely satisfied to see the speed and professionalism with which the Hella organisation have picked up and taken the Hella Pagid braking range to market and in the consistently positive response and acceptance from all markets to the Hella Pagid range, marketing and approach.
We are very excited to see the continued development of our JV business with Hella, and look forward to seeing Hella Pagid becoming a global brand leader in brake friction.
The need for weight reduction is talked about in every component sector yet aren’t friction materials already lightweight? Or is there further room for weight reduction?
Friction materials are already lightweight due to the build and low density of the raw materials. However, the carrier plates for the friction materials are made from “stamped steel” bringing with it some weight. Here weight saving is to be gained. The heavy parts in a brake system are the caliper and disc, not the brake pad as such. By improving the lifetime of the friction material calipers and discs can be resized to save weight, this can be a big gain.
We are seeing automakers showing a preference for front disc and rear drum brakes on most A and B segment cars while most C segment and above vehicles tend to have four wheel disc brakes. How do you see the further application of disc brakes across these lower segments? And how does that compare to the situation in emerging markets?
We are not expecting any major changes in the application of disc brakes in the aforementioned segments. This assumption also holds for the emerging markets. The application preference has been fairly constant over the last years and is likely to continue to be so.
I guess reducing stopping distances and weight reduction will always be a priority when it comes to design and development of braking systems, yet to what extent is improving the brake feel important?
The brake feel is part of a vehicle’s DNA. A BMW feels completely different from a Toyota which feels completely different to an Audi. The steering, the suspension and the brake feel are tied in together and become the main drivers for the ‘driving experience’ of a specific vehicle. But at the end of the day the driver must have 100% confidence in the brake system and therefore the brake systems’ role in the driving experience is important indeed.
In what ways has the growing use of electronic control affected braking hardware?
Electronics over the last ten years have revolutionised brake systems with the introduction of ABS, ESP and so on. For the brake pad this means changes to its normal working day. Brake pads have had to be significantly modified to cater for these additional demands. New demands are still entering such as electronic park brakes and for the future brake by wire brake systems also sometimes called dry brake systems by the removal of the hydraulic pump and pipes to be replaced by wires and electric motors.
With weight reduction in mind, to what extent are you seeing greater use of aluminium in disc brakes?
We now see aluminium brake discs on rear axle applications, TMD is supplying today these products. Aluminium calipers have traditionally been used for performance cars, now for the first time due to weight saving targets they are being introduced into mass market cars, this is a big change for the industry and a huge challenge for the friction material in terms of NVH.
As far as trucks and buses are concerned, high frequency brake squeals are commonplace. Could you draw on an example where you have made some improvements in that area? i.e. how did you achieve it and what were the issues (materials and construction) involved?
The remainder of this interview is available on just-auto’s QUBE research service