Based in Oxfordshire, UK Zircotec is a specialist coatings company that produces a range of proprietary plasma-sprayed metal and ceramic coatings to protect materials from the damaging effects of heat, abrasion and wear. Over the past year, Zircotec has been working with Aston Martin to provide thermal management solutions for its exclusive new supercar, the One-77. Matthew Beecham talked with Terry Graham, managing director of Zircotec to find out how their products were used in the supercar.
We have just seen the announcement that Zircotec products were used in the construction of the Aston Martin One-77. Could you tell us how that came about?
Zircotec has worked with Aston Martin in the past by providing thermal barrier coatings for the tailpipe on their DBS. With the One-77 created to epitomise the best in Aston Martin engineering, the design team used lightweight carbon fibre components and bodywork, which required protection from heat sources. Zircotec has a patented technology by which it can plasma-spray its proprietary ceramic based coatings onto composites. This enabled Aston engineers to use lightweight carbon fibre in sections of the supercar where the levels of radiant and conductive heat would otherwise prevent their use.
Why was the Zircotec composite coating so important for enabling the use of carbon fibre in the One-77?
Without a thermal barrier coating or heat shielding, the carbon composites in the One-77 would be damaged by the high temperatures found within the engine compartment. Delamination and resin melt are the common effects of composite heat damage which make its long term use in high temperature environments unsustainable. Using our thermal barrier coatings helps engineers to specify lighter materials that can meet performance or efficiency targets.
With a nod to F1, Aston Martin blows hot exhaust gases through the diffuser and Zircotec supplied a thermal barrier coating here too. Zircotec supplied many of the coatings that enabled F1 teams to exploit the blown diffuser technique. For OEMs we offer a coating that would allow hot gases to pass through the diffuser without causing damage. Our coating is smart and discrete with a number of colour options, so it is aesthetically pleasing too. We are able to apply the coating only where it is needed so we minimise weight gain too.
How well do you really know your competitors?
Access the most comprehensive Company Profiles on the market, powered by GlobalData. Save hours of research. Gain competitive edge.
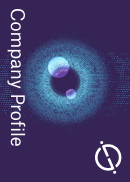
Thank you!
Your download email will arrive shortly
Not ready to buy yet? Download a free sample
We are confident about the unique quality of our Company Profiles. However, we want you to make the most beneficial decision for your business, so we offer a free sample that you can download by submitting the below form
By GlobalDataIf composites are vulnerable to heat why not use different materials?
Simple answer: weight. While steel and aluminium are more resistant to heat than carbon composites, their extra weight makes exclusive use of such materials undesirable. Performance can be blunted and efficiency is lost. Using traditional heat shields also prevents airflow around the part. As a coating we can maximise the air gap around the component which is better for cooling. Our coatings for carbon composite are typically only 0.2mm thick, so they take up very little space and add little in terms of weight. They also offer a smooth and aesthetic finish that allows good air flow and is in keeping with the required finish.
How is the coating applied?
All parts are processed at our UK facility. We plasma spray and in effect weld, the coating to the substrate. Our ceramic based material is fed into a plasma flame where it is melted and fired at around twice the speed of sound onto the substrate. By careful choice of parameters the substrate remains undamaged. Zircotec’s technology provides the durability needed to meet the OEM lifetime tests.
To make effective use of Zircotec’s coatings, are OEMs required to develop their cars with such thermal coatings in mind or can composite coatings be applied after manufacturing has begun?
One of the advantages of our plasma-spray process is it enables ThermoHold coatings to be easily applied to virtually any component, composite or otherwise. This means that while the advantages of Zircotec’s thermal coatings can be maximised at the design stage, it is also possible to specify them at a later stage to solve a heat issue that may only appear late on in development. We are also seeing some OEMs looking at the coatings as a means of differentiation. Having alternatively coloured tailpipes is a good way to refresh a car or highlight a performance model.
Currently the use of carbon composites are the reserve of motorsport and supercars, do you see the wider automotive industry adopting composite materials as a future alternative to steel and aluminium?
Currently the production of carbon composites is quite costly and relatively low-capacity, meaning such materials are usually seen in exclusive and expensive cars. But, the continued refining and development of existing and new manufacturing processes along with the fact that composite materials can be easily recycled, could see carbon composites becoming more affordable for OEMs creating everyday road cars.
The remainder of this interview is available on just-auto’s QUBE research service