
Saietta has engineered a breakthrough in electric propulsion motors for all vehicles from scooters to buses. It recently received funding from the UK’s Advanced Propulsion Centre (APC) enabling them to fast-track the production process and create 250 jobs. To learn more, we spoke to Wicher Kist, CEO of Saietta.
Could you give us some background to Saietta?
Saietta Group evolved from Agility Global, a company formed in 2008 to engineer premium electric motorbikes. Saietta actually means ‘thunderbolt’ in the Italian dialect of the founder’s parents.
When I joined Saietta in 2017 I made the major strategic decision to pivot the business to focus on developing motor technology that would power a broad range of electric vehicles (EVs) of the future, rather than bringing a single premium e-motorbike to market. If you look at how the market for EVs is now exploding, we made the right choice.
Could you tell us about your Axial Flux Traction electric motor? What have you done differently?
We went back to the drawing board when it came to our proprietary Axial Flux Traction concept, and we’ve spent the last four years getting its design spot on and working out how to best attack the issue of mass mobility at the right price. Saietta’s AFT topology is a yokeless axial flux machine but, innovatively, it uses a distributed winding with overlapping coils. This minimises core and magnet losses, yielding high efficiency over a broad range of speeds and torque.
How well do you really know your competitors?
Access the most comprehensive Company Profiles on the market, powered by GlobalData. Save hours of research. Gain competitive edge.
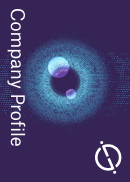
Thank you!
Your download email will arrive shortly
Not ready to buy yet? Download a free sample
We are confident about the unique quality of our Company Profiles. However, we want you to make the most beneficial decision for your business, so we offer a free sample that you can download by submitting the below form
By GlobalDataWe have a family of motors suited to voltages between 48V and 120V, each with a dry weight of just 16kg.
All this means we now have a family of motors suited to voltages between 48V and 120V, each with a dry weight of just 16kg – something we’re really proud of. Peak torque is as much as 150Nm, with rated continuous torque of 50-60Nm and continuous power output between 12 and 23kW, depending on voltage. Higher power applications can be achieved by simply stacking motors alongside each other on a common driveshaft, and work is underway for an 800-volt system, too.
What materials are used in the AFT’s construction?
Axial flux motors have long been recognized as a superior solution for electric traction, particularly for lightweight vehicles, because of their inherently higher torque density. However, if you’re looking at that sector you’ve got to consider the cost of the motor versus the vehicle BOM. Saietta’s unique design features low-cost core components which can be assembled in a highly automated way in mass production.
Essentially, the motors feature low-cost copper wire in an extruded aluminium stator, sandwiched between cheaper, unsegmented, magnets set into mild steel rotors. The AFT stator is fully encapsulated by an epoxy resin to create a robust composite structure with good thermal performance which, in conjunction with the external water jacket, gives the motor a high continuous power rating over a wide range of ambient temperatures.
Can you simulate a motor design before making it?
Absolutely, but that’s just one part of what we can provide our customers. We can work from market research into competitors and sanity checking the concept and then simulating the full vehicle before it’s built. We can then build prototype motors and test them rigorously to ensure they deliver as required.
It doesn’t stop there, because we also get questions like: ‘we don’t have the capacity to build a prototype vehicle,’ or ‘we have a board presentation, and we need to have a running vehicle.’ We can take on the full build of that prototype vehicle. Because we have all that we need in-house at our base in Oxfordshire, we can tailor the exact design of the motor to the specific requirements of the application. In essence, we’re a one-stop-shop.
Which geographical markets are you targeting?
This is something that we thought very carefully about. Saietta’s launch motor was actually designed for what’s known as the ‘L Category’ sector which includes final mile delivery vehicles, rickshaws and motorcycles. Globally motorcycles alone amount to some 63 million registrations per annum which is independently forecast to rise to 126 million per year from 2030 with 40 per cent of these being electric. That’s some 50 million electric motorbikes being sold every year from 2030.
These are parts of the world that really stand to benefit from the rapid improvement of urban air quality through a switch to EV’s, but they have to be affordable. Our solution will allow highly effective EVs to be introduced at competitive price points to the current ICE models.
You mentioned your facility in the UK, is your intention to keep production in the UK, or will you look to build motors somewhere cheaper?
Our base in Oxfordshire means we have a lot of space to play with, which includes 20 miles of private test track. We’re planning on increasing production capacity within our existing facilities as well as investing in more R&D and motor test facilities. Last year’s APC grant is allowing us to fast-track the ramp-up of production and trigger a very significant increase in our team of highly skilled engineers over time. Longer term we expect to be producing motors for clients, as well as licencing production to those clients who can manufacture locally. In this way, we’ll be able to help them minimise costs and introduce break-through EVs to market sooner.
What are you working on next?
Looking beyond the two and three-wheel market, we can see significant opportunities coming from global Governmental legislation to ban the sale of new internal combustion engine cars from 2030. Obviously, the form factor of our motor is shaped like a wheel, so we are looking at proactively developing in-wheel motor variants in a number of live projects. This includes the development of a new ‘skateboard’ platform which significantly increases load capacity in a smaller footprint – great as a delivery vehicle in busy towns and cities.
We’ve also retrofitted a Saietta motor into a first-generation Renault Twizy as a proof of concept. In comparison with the original vehicle, the usable range increased by 20 per cent, with improved driveability. With the development plans in place for various automotive applications, the company is extending its motor range to include marine applications and wind turbines. The sky is the limit.