BASF says it now offers a new module for simulating applications of injection-molded components and that this offers benefits – in particular – in developing components for future electric vehicles.
BASF’s Ultrasim simulation tool delivers precise calculations of the anisotropic mechanical behaviour of fibre-filled plastics after manufacturing in the injection-molding process. But another service has now been added: a thermomechanical model for fibre-reinforced thermoplastics now enables precise forecasts of temperature-dependent deformation via simulations.
One major benefit for customers is that they can now identify possible weak points virtually during the actual development phase for components and prevent them before the start of the series production phase. The new module considers the complex thermomechanical material behaviour, the impact of the anisotropic fibre orientation as well as temperature distributions and changes in the component.
“During the early development phase, it is absolutely essential to make detailed forecasts for the end product,” says Andreas Wonisch, simulation expert at BASF. “Particularly with high-performance plastics that are used in cars and are exposed to huge temperature differences, possible deformations need to be predicted.”
Fibre-filled plastics display very complex thermodynamic behaviour. Under a thermal load, there may be undesired deformations which depend on the local temperature and fibre orientation in the component. This is especially critical for E&E components with integrated switching elements. The highly sensitive electronics must not sustain any damage. Exact prediction of the thermal deformation with prior simulation using Ultrasim thus saves time and money in the development process.
Integrative approach to simulation with Ultrasim
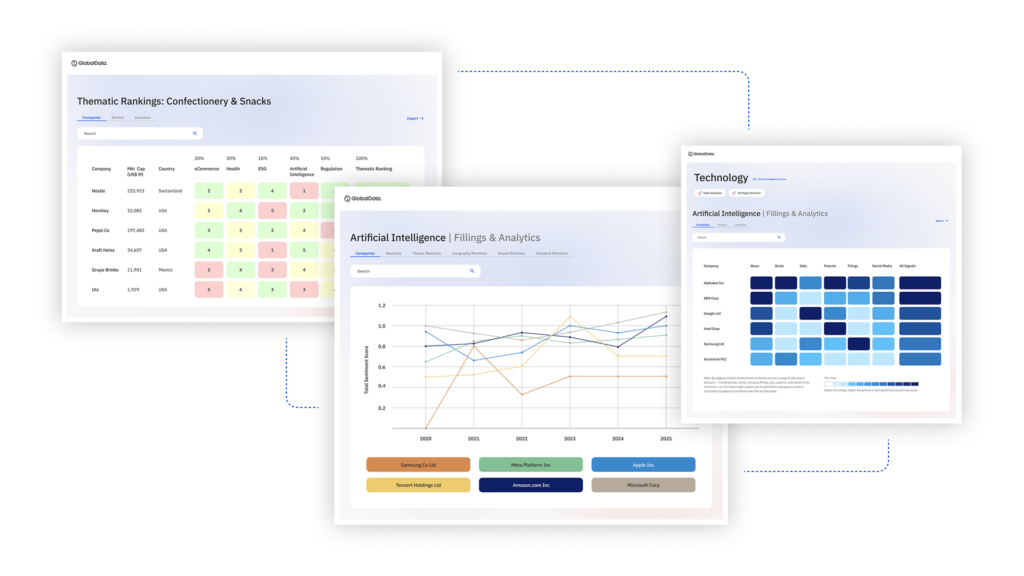
US Tariffs are shifting - will you react or anticipate?
Don’t let policy changes catch you off guard. Stay proactive with real-time data and expert analysis.
By GlobalDataWith extensive measurements directly on the material and on injection-molded test specimens, Ultrasim offers comprehensive material characterisation across the full temperature range. Instead of simulating at one single temperature it is possible to recalculate the typical temperature load from -40 to 150°C for various applications. The influence of the fibre orientation in the component, which results in anisotropic thermomechanical behaviour, is considered through integration of the process simulation.
This allows for a much more comprehensive simulation, taking account of the rheological and thermal properties and the fibre orientation from the injection-molding process. The consequence is that component faults are identified and avoided at an early stage. BASF already uses the calculation model for a large number of applications, primarily for the automotive industry.
Automotive OEMs benefit from precise simulations
The issue of electric mobility presents great challenges for the automotive sector, BASF notes. New and innovative components that need to protect highly sensitive conductor tracks, sensors or circuit boards are being developed. With severe temperature differences, no deformations to the components and thus damage to the electronics should occur. The new Ultrasim module has already been successful with different parameters in various customer projects, for example a control electronics system. The simulation of thermal expansion for housings of electronic control units (ECUs) displayed very good conformity across the whole temperature range that was investigated. Other possible uses of the simulation tool would be for plastic components in headlights in which extensive power electronics are used and heat dissipation has an effect.