
China’s Contemporary Amperex Technology Company Limited (CATL) officially launched its newly in-house developed, ultra-safe battery electric vehicle (BEV) chassis, which it plans to make available commercially to local vehicle manufacturers.
The world’s largest electric vehicle (EV) battery manufacturer unveiled the “Bedrock Chassis,” which it claims can withstand 120 km/h frontal impacts without catching fire or exploding. The company said the ultra-safe Bedrock Chassis sets “a new standard for intelligent chassis safety, providing comprehensive protection across all scenarios and speed ranges.”
The Bedrock Chassis, which is based on a battery-centered skateboard design, uses “Cell-to-Chassis” integration technology, which directly integrates the battery cells into the chassis and allows for a shared structural design. Using a body-on-chassis design, CATL claims the Bedrock Chassis can absorb 85% of the collision energy of a vehicle compared with around 60% in standard BEV chassis designs.
The company pointed out that “through various technological breakthroughs, the Bedrock Chassis successfully passed the world’s first highest speed + strongest impact dual extreme safety test. This achievement enables the chassis to pass the 120 km/h frontal central pole impact test without catching fire, exploding, or thermal runaway, redefining the benchmark for safety in the industry.”
Most frontal impact safety tests carried out today are based on the C-NCAP’s (China New Car Assessment Program) 56 km/h test. CATL claims this is the first time a BEV has been put through a 120 km/h frontal impact test, which it says is equivalent to a fall from a 56-metre-high building, generating a collision energy 4.6 times that of a 56 km/h collision.
CATL said the Bedrock Chassis uses “a revolutionary three-dimensional biomimetic tortoise shell structure, where the body and energy unit framework are integrated, deeply coupled to provide the energy unit with indestructible protection,” which it says “disperses impact forces across multiple pathways during a crash, gradually decelerating the vehicle and significantly reducing the depth and speed at which obstacles intrude into the cabin.”
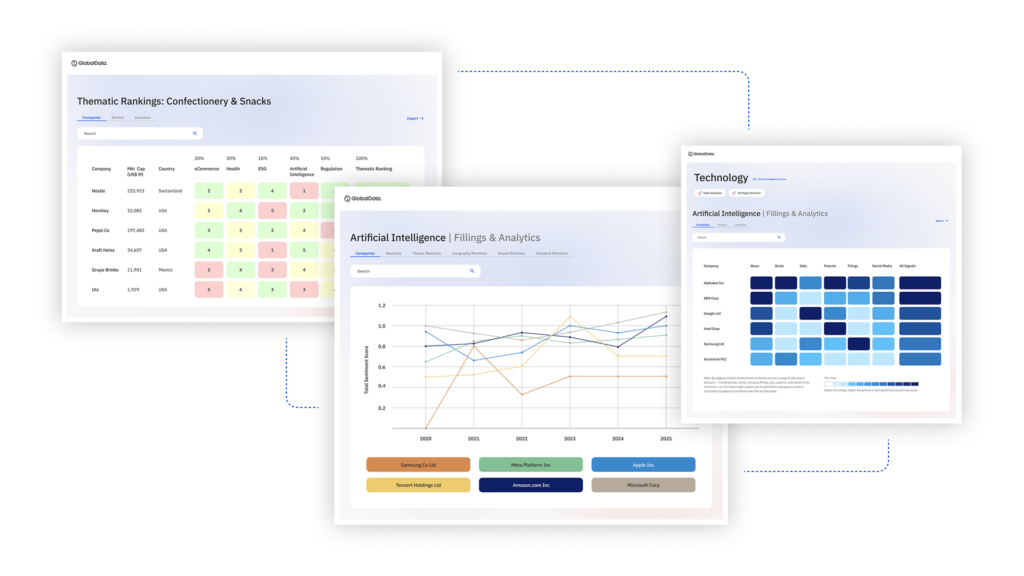
US Tariffs are shifting - will you react or anticipate?
Don’t let policy changes catch you off guard. Stay proactive with real-time data and expert analysis.
By GlobalDataMaterials used include “submarine-grade” hot-formed steel with a strength of 2000MPa, “aerospace-grade” aluminum alloy with a strength of 600MPa, and multiple barrier structures to further enhance the chassis’ rigidity.
The chassis also incorporates an ultra-safe battery cell design, called NP technology, and a high-ductility energy-absorbing insulation film. It achieves disconnection of the high-voltage circuit within 0.01 seconds of impact and completes the discharge of residual high-voltage energy in the vehicle within 0.2 seconds, which the company says is a new industry record.
The first automaker to use CATL’s Bedrock Chassis will be Avatr Technology, a joint venture between Changan Automobile, Huawei and CATL.