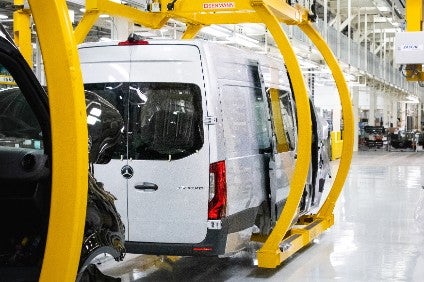
The US launch of Daimler’s 2018 Mercedes-Benz Vans Sprinter follows the opening of a much expanded assembly plant in North Charleston and a switch from semi knocked-down (SKD) to completely knocked-down (CKD) importation requiring new body and paint shops.
After “considering the high market potential for the new Sprinter in North America”, Daimler decided back in March 2015 to build a new factory in time for the 2018 model launch.
The plant in North Charleston, South Carolina, is the result of two years’ construction at a cost of US$500m and employs 900. The automaker said that number would grow at the now expanded site to 1,300 by the end of 2020. Suppliers would create an extra 600 new jobs in and around the area.
The factory started assembling SKD Sprinter kits in 2006 and, in 2015 added Metris [Vito] midsize models. Earlier Sprinters were marketed under the Freightliner badge (with an emphasis on ‘US made’) and the third generation will also be offered as a Mercedes line.
For CKD kit assembly, the plant now has body and paint shops and extended final assembly as jigging, welding, coating, wiring, glazing and trimming is all now done in the US.
Expansion has tripled factory footprint to 222 acres or nearly 10m sq ft. The production and office building area is now around 41 acres or 1.8m sq ft, supplemented by free and logistics space. Connectivity and digital communication have been added for flexibility and efficiency and to cope with the increasing variety of vehicle variants while sales volume continues to rise.
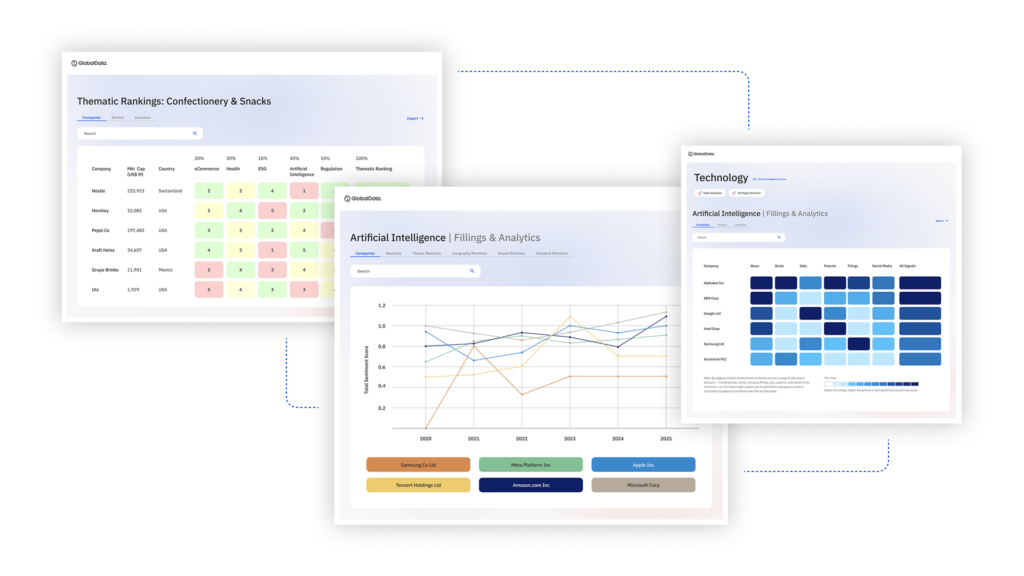
US Tariffs are shifting - will you react or anticipate?
Don’t let policy changes catch you off guard. Stay proactive with real-time data and expert analysis.
By GlobalDataDigital and driverless
Increased digitalisation also helps workers as it minimises routine and repetitive tasks, giving them more time for higher-value work. Innovations include self-driving transport systems, the shift to paperless, digital communication and virtual employee training.
The plant also is equipped with driverless transport systems which can travel around 40 miles (70km) in one shift. They are controlled through networking with the plant’s IT system and via RFID (radio-frequency identification). The associated transponders, incorporated into floors, receive the necessary driving commands. The vehicles can also use Bluetooth to communicate with one another and coordinate automatically.
RFID
Daimler said paperless, digital production documentation, based on RFID technology, was one of “the biggest transformations”. It allows the position of a specific component to be pinpointed precisely by a contactless method enabling automatic identification and tracking. This allows employees in logistics and production to adjust to process changes while quality assurance personnel can check the correct part has been installed in the right vehicle. RFID has made it possible to eliminate several steps of documentation – one example the manual scanning of barcodes. This saves time and cost and also reduces potential sources of error.
Digital tool training
Conventional training methods are supplemented by digital to help prepare workers for their jobs. Due to the variety of body types, powertrains, body lengths, payloads, cargo space heights and equipment options, the new van is available in more than 1,700 variants.
Each employee has to learn around 900 individual process steps in a specific order to build the new vehicle. In assembly, employees can use an on-screen approach similar to that of a computer game to familiarise themselves with procedures and components. Previously, such training was conducted only on pre-production vehicles.
Training of paint-shop personnel is also aided by digital techniques as trainees use virtual reality goggles and paint guns for realistic simulation of the painting process.
“The US is already the second largest market for our Sprinter today. With the new [factory], we will be able to supply our customers in North America even faster and with more flexibility in the future. This makes better use of the dynamic market potential, placing our new plant as a central component of our growth strategy,” said Mercedes-Benz Vans chief Volker Mornhinweg.
“Our priority during the planning process for this facility was maximum flexibility. This enables us to react in an agile and anticipatory manner to current developments and customer desires. Additionally, it guarantees excellent quality within our proven, standardised production system,” said operations chief Frank Klein.
The automaker said it would build Amazon branded vans for the retail company’s new Delivery Service Partner programme. Small business owners will work with third-party fleet management companies to buy their customised vans and get special leases in order to keep their startup costs low.
Amazon said the programme had been so successful it had boosted its order to 20,000 vehicles.