
Renault Group has opened a new logistics facility in Villeroy which is 100% automated and equipped with a system from Exotec, the French industrial robotics company.
This collaboration was said to be a world first for a car manufacturer. Skypod robots facilitate the work of operators by picking items at height thereby eliminating the risk of falling. The time it takes to prepare parts orders is thus divided by six and the surface of the storage area on the site is reduced.
“We will be able to increase by 25% the number of orders served and strengthen our commitment to customer satisfaction, which remains a priority for us,” said Xavier Lhors, director of after sales logistics at Renault Group.
Exotec’s logistics systemis distinguished by its flexibility and adaptability to changing production needs and is able to adjust in real time with the addition of storage modules, robots or the modification of conveyors.
The robots are autonomous and equipped with advanced navigation and handling capabilities. Their compact design and their agility allow them to move quickly and efficiently in complex logistics environments, especially in the presence of other equipment and workers.
Currently, 191 robots are deployed at the Villeroy site according to specific requirements, whether for picking, inventory, put away or compaction.
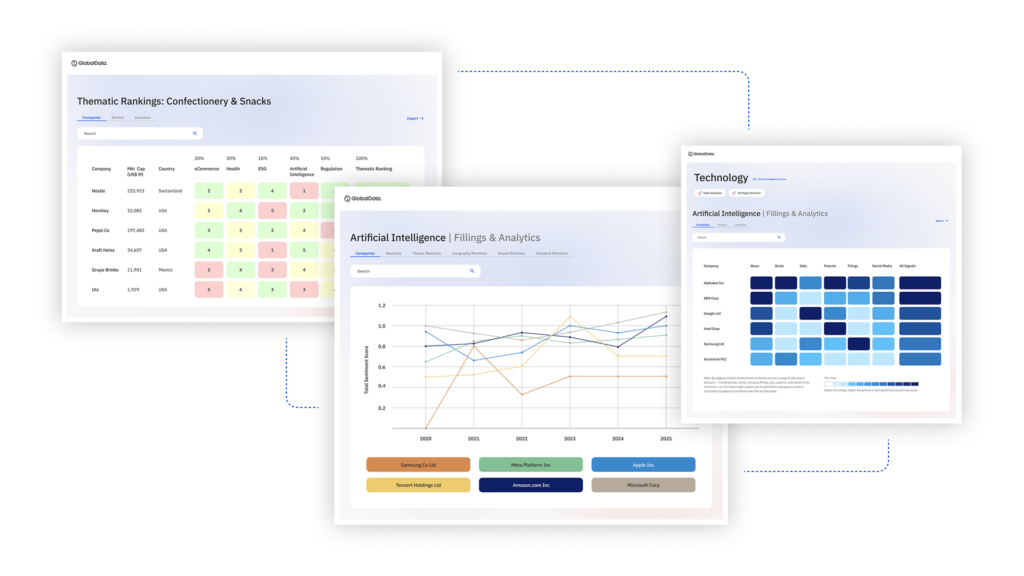
US Tariffs are shifting - will you react or anticipate?
Don’t let policy changes catch you off guard. Stay proactive with real-time data and expert analysis.
By GlobalDataRobots now play a central role, from managing the storage of trays to making them available to operators for order preparation.
Pallets for storage in the facility are automatically injected into 60 litre trays. These are then transported by a robot that places them in the storage racks.
When customer orders are received, picking tasks are assigned to picking stations. A robot then collects the reference of the items ordered to bring them to the picking stations. This operation is repeated for each item ordered.
Once the items are prepared, the packages are transported to the shipping area where they are sealed and routed to shipping docks to be loaded onto trucks.
The facility can prepare 4,000 order lines per hour at peak activity with 14 picking stations.
The preparation time of an order (from the beginning to the delivery of the package to shipments) is 20 minutes. Previously, this took two hours.
The automation reduce the site’s energy consumption by 30% compared to the traditional system thanks to the elimination of handling equipment, replaced by robots that consume less energy.
Villeroy currently processes up to 40,000 order lines per day with 110,000 references, including 20,000 references managed by the new logistics tool.