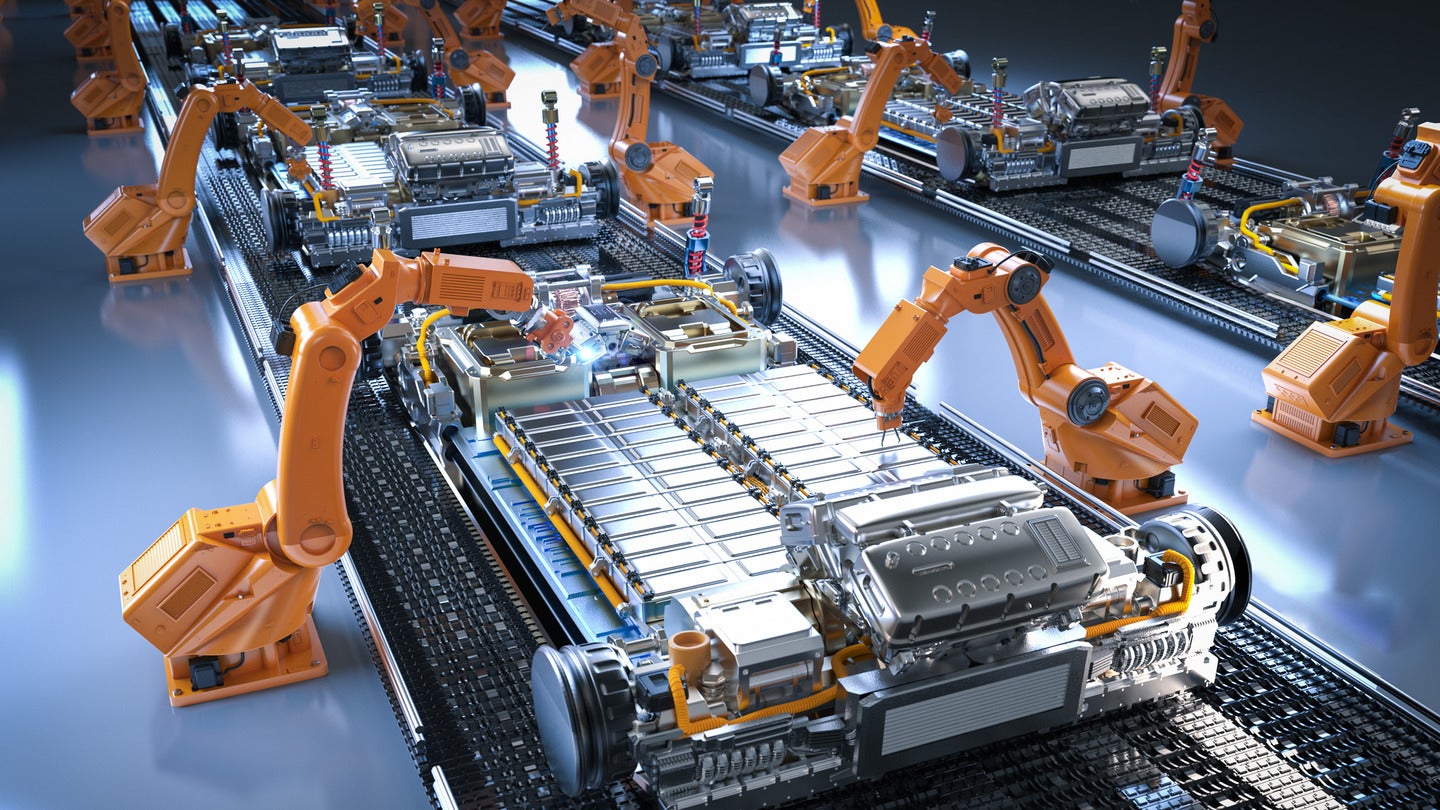
Dutch automaker Stellantis announced on 24 October that it had signed a memorandum of understanding with US-based Orano to establish a joint venture for recycling end-of-life electric vehicle (EV) batteries. The move, Stellantis said, is calculated to strengthen the company’s position in the EV battery value chain by granting them “additional access to cobalt, nickel and lithium necessary for electrification and energy transition.”
This is just the latest in a series of joint ventures between automakers and EV battery recycling firms, as the former seek to shore up their supply chains against projected raw material shortages and boost the environmental, social and governance (ESG) profiles of their batteries.
Earlier this month, South Korea’s Kia established a public-private partnership with North Gyeongsang Provincial Government and Gyeongbuk Technopark to build a battery recycling ecosystem, and, last month, Volvo announced a partnership with Newcastle-based Connected Energy to recycle its commercial EV fleet batteries.
And the list goes on. Earlier this year, Honda inked agreements with two leading US-based battery recycling companies, Cirba Solutions and Ascend Elements, in a move calculated to bring the automaker closer to its 2050 carbon neutrality goal. Indeed, Andreas Breiter, partner at the global management consulting firm McKinsey & Co., notes that using recycled battery materials for EV batteries equates to approximately 25% lower carbon emissions versus virgin mineral extraction.
In March, meanwhile, Germany’s Mercedes-Benz joined forces with three Chinese companies, including China’s largest battery maker CATL, to form a “closed loop” battery recycling project.
At present, China accounts for almost all EV battery recycling, claiming the lion’s share of an $11bn market. The industry has been bolstered by heavy government R&D investment and incentives for domestic manufacturers and has promoted lithium-ion battery recycling through policy since 2012. Lithium recycling was even noted as a key priority in the Chinese government’s latest five-year development plan, as the country seeks to decrease its reliance on overseas imports.
ROW plays catch-up with China in EV battery recycling
The rest of the world is now playing catch-up with China. Little-known provisions in the 2022 US Inflation Reduction Act, for example, have spurred a surge in the construction of battery recycling facilities in North America by making US-recycled battery materials eligible for subsidies, as the US seeks to decouple EV battery production from Chinese supply chains.
The EU and UK, by contrast, have become less attractive destinations for battery recycling, focusing on mandates regarding minimum amounts of recycled materials in future EV batteries rather than financial incentives.
The EU has also instituted its End-of-Life Vehicles Directive, which mandates that automakers take back vehicle owners’ end-of-life batteries, and its Fit for 55 package, which requires the publication of battery carbon footprints.
Honda’s partner, Ascend Elements, has begun construction on the first phase of a $1bn facility in Western Kentucky to harvest materials from old batteries, after having received a hefty $500m in Energy Department grants, while other battery recycling plants have popped up across the newly christened “Battery Belt”, including Redwood Materials’ $3.5bn South Carolina plant. Redwood Materials has established numerous “closed loop” partnerships with Volkswagen, Ford, Volvo and Toyota. Honda’s other partner Cirba Solutions already has five plants in the US and a facility in Canada, and has a $340m South Carolina facility, which is set to be operational in late 2024.
By contrast, Altilium Metals is currently the UK’s only company recovering lithium, nickel and cobalt from waste EV batteries. The company opened its first industrial-scale battery recycling plant earlier this year in Tavistock, Devon, while another full-scale processing plant is planned for 2026 in Teesside.
In early 2022, mining giant Glemcore and EV battery start-up Britishvolt announced a joint development of a new UK battery recycling plant in East London, which was scheduled for launch this year. However, Britishvolt’s collapse into administration at the beginning of the year and its failure to find funding makes this plan look increasingly unlikely.
CEO of Ascend Elements Mike O’Kronley told the BBC earlier this year that in order to compete with the US on battery recycling, the UK must implement a similar level of incentives and create a more favourable legislative environment.
Recyclers split over which EV battery chemistry will prevail
Battery recycling remains a nascent industry the precise contours of which have yet to be determined. A key area of uncertainty for battery recycling companies is which cathode chemistry will prevail in future EV battery development, making future planning more challenging.
The majority of EV batteries currently use cathodes composed of NMC (nickel manganese cobalt) or NCA (nickel cobalt aluminium). However, cathodes containing LFP (lithium iron phosphate) have been gaining traction for standard-range EVs, with LFP batteries now making up 30% of the market in 2022, according to the International Energy Agency (IEA).
Tesla has begun producing a lower-range and less-expensive EV that uses an LFP battery and revealed in October 2021 that it would switch to LFP batteries for all its standard-range vehicles globally. Ford, Rivian and Volkswagen have also unveiled plans to use LFPs in North American cars, while General Motors has expressed an interest too.
The key constituents of batteries’ cathodes will have significant repercussions for the viability of certain EV battery recycling business models. Batteries that are currently being retired contain large amounts of cobalt and nickel – two highly valuable materials – whose sale amply covers the cost of recycling.
Studies show, however, that the increasingly popular LFP lithium-ion battery is currently unprofitable to recycle due to low revenues from material recovery and the expense associated with hydrometallurgical recovery of complete metal ions. Traditional pyrometallurgical and hydrometallurgical techniques also release gases that are toxic to the environment.
One solution, suggested by the Union of Concerned Scientists, might lie in extended producer responsibility schemes, which would make OEMs responsible for designing LFP batteries that are easily and efficiently disassembled. Another lies in further recycling innovation.
Encouragingly, GlobalData’s patent analytics show that the drive for new EV battery recycling techniques and technologies is well underway, with the number of patent applications and grants reaching 110,118 in 2022 compared to 80,505 in 2018.
A GlobalData poll on Just Auto published early last year, meanwhile, found that a majority of respondents believe solid-state batteries - unlike the liquid- or gel-based batteries typically available now - could be available for EVs within five years. Of 917 respondents, 33.5% believed they would be available within three to five years and a further 27.2% believed within less than three years.
Our signals coverage is powered by GlobalData’s Thematic Engine, which tags millions of data items across six alternative datasets — patents, jobs, deals, company filings, social media mentions and news — to themes, sectors and companies. These signals enhance our predictive capabilities, helping us to identify the most disruptive threats across each of the sectors we cover and the companies best placed to succeed.