Production of the new 2014 Chevrolet Captiva is underway at General Motors’ Rayong assembly plant in Thailand, with dealer deliveries scheduled to begin later in June.
GM says that the SUV is the latest model to benefit from GM’s “built-in quality principle and processes, which help ensure a worry-free ownership experience”.
“Several years ago, we took the best practices from each of our regions and integrated them into our current built-in-quality strategy. This strategy moves quality into the build process by ensuring quality defects are prevented at each and every step of the assembly process, rather than trying to detect quality defects on the finished product,” said Michael Perez, vice president of manufacturing for GM Thailand/SEA Operations.
The traditional approach in the industry was to conduct quality inspections before vehicles leave the plant. This containment approach has several weaknesses. It depends on the ability of quality inspectors to spot problems and requires undoing faults by dismantling and refitting the vehicles. With built-in-quality strategy, the customers receive the highest quality finished vehicle when the company performs each step of the assembly process right the first time.
“With quality pillars, we control the quality in each step of the build process,” Perez said. “It is critical to get every single step right the first time, every time.”
Quality Pillars are categorised focus areas based on feedback from external and internal customers, or Voice of Customers (VOC), which is central to the quality Pillars. The principle is best summarised by its mantra – do not accept, build or ship a defect. Each of the four shops in GM’s vehicle assembly facility has its own set of quality Pillar’s to ensure defects are prevented.
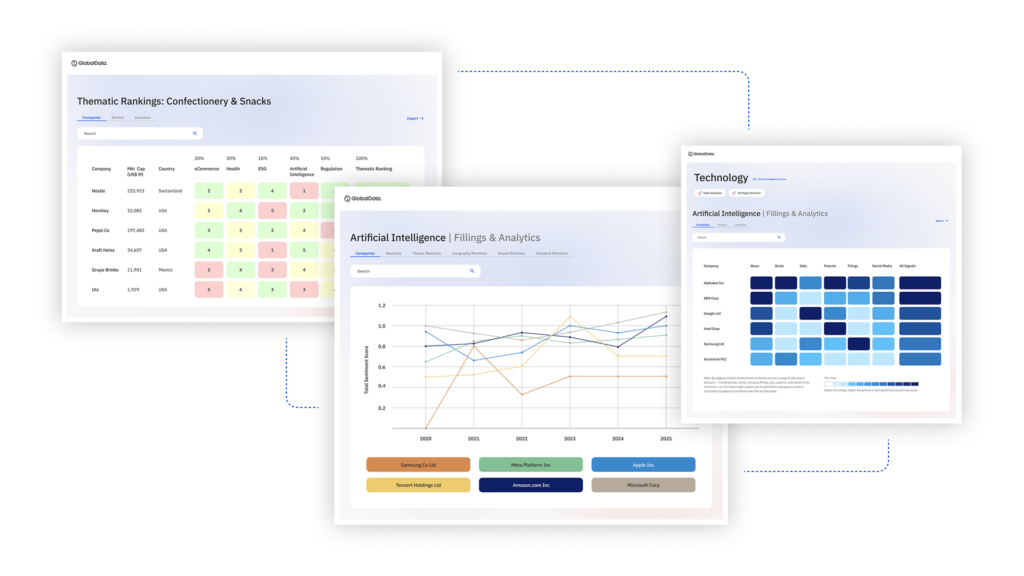
US Tariffs are shifting - will you react or anticipate?
Don’t let policy changes catch you off guard. Stay proactive with real-time data and expert analysis.
By GlobalDataBuilt-In Quality starts in the Press and Body Shop where metal sheets are pressed to form Captiva’s body panels and welded together. The body ‘shell’ then gets a coat of colour and gloss at Paint Shop while trimmings and interior fittings are assembled at General Assembly Shop.
Unchana Surathikhajon, director of GM Thailand and Southeast Asia warranty, customer satisfaction and regional quality said, “At the plant level, cross-functional meetings are regularly held to ascertain how feedback can be disseminated to the shop floor and incorporated as processes.”
The nature of how the quality pillar’s processes are developed also means processes are constantly evolving and improvement is continuous. In other words, good quality can only get better.
In addition to customers and dealers, feedback is also provided by third party surveys. Feedback not only highlights opportunities for improvement, but also provides support and endorsement from customers of the things that are being done correctly. Chevrolet’s quality efforts have resulted in the Captiva being named best-in-class in the SUV segment in a leading consumer study.
“Not only do we want to build defect-free products in our teams and stations in the plant,” Perez said. “Our goal is to prevent defects by design in the first place.”
GM’s facility in Rayong has produced more than 1m vehicles to date, starting with the Chevrolet Zafira MPV in 2000, a model still common on Thailand’s roads today. Quality has been an integral part of every vehicle that has left the line, starting Zafira to the latest new 2014 Captiva, GM maintains.