Quality control of the new Land Rover Discovery 3 to be launched this autumn will be aided by the recent installation of eight car body co-ordinate measuring machines (CMMs) at the company’s Solihull factory. They were built and installed by LK Limited, which believes the CMM order was the largest placed in the UK.
Currently, the computer-controlled machines are supporting the continuous production phase-in of the new vehicle, 24 hours a day, five days a week. They confirm that critical characteristics are continuously monitored and maintained on all car body sub-assemblies.
Two twin-column HC-90 measuring machines have been integrated into the body-in-white production line, this being a first for Land Rover. They allow one in four underbodies and a similar number of bodies-less-doors to be inspected in the production area, enabling a higher frequency of measurement than the off-line facilities allow. In-line inspection therefore provides a more representative level of data acquisition to ensure dimensional stability of the vehicle. Measuring cycles are restricted to key body construction points and are relatively short at around six minutes.
An additional task of these CMMs is to ensure the accuracy of geometric pallets on which the car bodies are assembled. Previously, verifying that the pallets were within tolerance was carried out in an off-line CMM facility and entailed taking them out of the body-in-white line at weekends to avoid disrupting production.
Off-line body-in-white inspection at Land Rover has benefited from the installation of twin-column HC-90 and LY-90 machines, as well as a quad-column version of the latter. Trim and final inspection activities have been enhanced by another LY-90 twin-column model, making a total of 14 individual CMMs within the eight new measuring cells.
How well do you really know your competitors?
Access the most comprehensive Company Profiles on the market, powered by GlobalData. Save hours of research. Gain competitive edge.
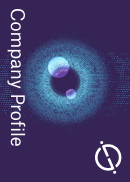
Thank you!
Your download email will arrive shortly
Not ready to buy yet? Download a free sample
We are confident about the unique quality of our Company Profiles. However, we want you to make the most beneficial decision for your business, so we offer a free sample that you can download by submitting the below form
By GlobalDataOne of the functions of the off-line inspection facility is to maintain quality control over closures (doors, bonnets and boot lids), which are inspected against a weekly measurement control plan. Cycle times are of the order of 15 to 30 minutes.
In addition, at the start and end of each shift, an underbody and a body-less-doors are taken out of production for off-line Level 3 checks, which take from one to three hours and include additional features such as the holes for locating the trim. The current weekly off-line measurement plan requires 165 sub-assemblies to be inspected, excluding in-line measurement. In addition, specific measurement is carried out for investigation purposes to provide dimensional data to the launch team, enabling potential build issues to be resolved.
LK undertook turnkey responsibility for the project, including foundations for the machines and preparing programmes for inspecting Land Rover Discovery 3 body sub-assemblies.
Using software working directly from CAD models, programmes were prepared while the machines were being installed and before first prototypes became available. All inspection cycles were ready to run when the commissioning phase started at Solihull.
LK engineers went on site at this stage to edit programmes to take account of engineering changes that had been made in the interim.
Nineteen metrology staff work in the new facility, of which four are devoted to portable measurement of the build fixtures. The remainder operate the LK CMMs across three shifts, with four or five operators and engineers in attendance per shift of which two provide skeleton cover for the subsequent shift.
Other companies within Ford Motor Company’s Premier Automotive Group also use LK CMMs.