DaimlerChrysler Corporation
is testing plastics recycling technology that could help make the company’s vehicles
95 percent recoverable within the next few years, significantly reducing the impact
of end-of-life vehicles on the environment.
If validated in a five-month
pilot project launched this month, the new recycling technology could reduce
by one-third the amount of automobile waste going into landfills, provide a
source for high quality recycled plastics that can be used to produce new automotive
parts, and result in significant cost savings in the production of new vehicles.
The project represents the
second phase of DaimlerChrysler’s CARE (Concepts for Advanced Recycling and
Environmental) Car Program which has the dual goals of increasing the recyclability
and recovery of automobiles and the use of recycled materials in new vehicles.
“This project is not only
good for the environment, it is good business for DaimlerChrysler,” said Bernard
I. Robertson, Senior Vice President – Engineering Technologies and General Manager
– Truck Operations. “By recycling the plastics from old cars and trucks, which
today are simply dumped in landfills, we believe we can reduce the cost of producing
new vehicles by millions of dollars a year.”
If successful, the test
could also open the door to a profitable new market for automobile recyclers
in recycled plastics, polyurethane foams and copper. The three firms working
with DaimlerChrysler are: Recovery Plastics International of Salt Lake City,
Utah, which developed the automated, skin flotation process being used to separate
plastics from other automotive shredder residue; and automobile recycling companies,
New York-based Hugo Neu Corporation and David J. Joseph Company which has operations
in the United States and Europe. The project is due to be completed in early
2001.
About 95 percent of all
automobiles are recycled; however, recycling is generally limited to the 75
percent by weight of the vehicle that is metallic. The remaining 25 percent,
including a significant amount of plastics, has been very difficult to recycle
cost-effectively. As a result, most of that remaining material, known as automotive
shredder residue, is disposed of in landfills. The recycling equation is further
complicated by the fact that many automakers are using increased amounts of
plastics as a way to reduce weight and improve fuel economy.
How well do you really know your competitors?
Access the most comprehensive Company Profiles on the market, powered by GlobalData. Save hours of research. Gain competitive edge.
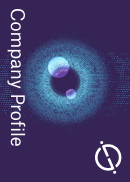
Thank you!
Your download email will arrive shortly
Not ready to buy yet? Download a free sample
We are confident about the unique quality of our Company Profiles. However, we want you to make the most beneficial decision for your business, so we offer a free sample that you can download by submitting the below form
By GlobalDataWith increased plastics
recycling made possible by the process under development at DaimlerChrysler,
up to 95 percent of vehicles by weight could be recycled and recovered. And
DaimlerChrysler would have a cost-effective source for recycled plastics that
can be used to increase the number of components made from recycled plastics
in new vehicles.
In April 1999, DaimlerChrysler
unveiled two Dodge Stratus sedans developed jointly with 26 supplier companies
that demonstrated the potential for increasing recycled materials in new vehicles.
More than 500 parts were modified to increase the content of recycled material,
including tires, seats, instrument panels, trim, floor mats, sun visors, fuel
tanks, air bag systems, seat belts, door handles, carpeting, fascias, tail lamps,
body trim, mirrors and underhood plastic applications.
As a result of the project,
vehicle weight was reduced by seven pounds and seven types of plastics were
eliminated, thus reducing the complexity of separating plastic components for
recycling. Up to 40 percent of the plastic materials used in the vehicles were
from recycled materials. At the same time, the vehicles met all requirements
for comfort, performance, quality, emissions and safety.
The two Stratus CARE Cars
have undergone extensive road testing to confirm the durability of the redesigned
parts. One of the vehicles was tested for 200,000 miles, the other for 100,000
miles. “The vehicles passed with flying colors. There were no failures in any
of the redesigned CARE Car components,” said Gerald Winslow, CARE Car Program
Manager.
Planning is underway to
incorporate ideas from the CARE Cars into future production vehicles. “To do
that, we will need a reliable source of recycled materials that meet our requirements
for quality and purity. This phase two pilot project can help us get there,”
said Susan Yester, Senior Manager – Vehicle Recycling Programs.