Chrysler Group’s Warren Truck Assembly Plant in Warren, Michigan, is operating three shifts to keep up with demand for recently redesigned Dodge Ram and Dakota pickup trucks.
Three shift, round-the-clock operation of an assembly plant is relatively rare in the motor industry. BMW’s Mini operation in Cowley, England, is operating three shifts seven days a week; the third operates at the weekend and well-paid jobs on it are keenly sought by students from nearby Oxford University. The PSA Peugeot-Citroen near Coventry at one time operated three-shift, 24-hour days during the week and added a fourth weekend shift to keep up with demand for the Peugeot 206.
The third shift at Chrysler’s Warren Plant, – creating about 900 new jobs – was added in early 2004. It naturally increased the plant’s capacity, but also improved its flexibility to accommodate the fully redesigned 2005 Dakota, meet changing customer demands, and add future product.
“Warren Truck is a model for flexible manufacturing. It has the ability to build numerous permutations of multiple body styles on one assembly line,” said Chrysler group manufacturing head Frank Ewasyshyn,. “Add to that one of the few plants operating 24 hours a day, up to six days a week, and you have a world-class facility, raising the bar for this type of operating schedule in the industry.”
While the addition of the third shift was one of the most significant transformations at Warren, other modifications have been made in anticipation of the launch of the new Dakota. New manufacturing technologies and processes were incorporated, including major changes to the cab and box framing and box sub-assembly areas, the body shop and the paint shop to accommodate the unique body panels of each vehicle.
How well do you really know your competitors?
Access the most comprehensive Company Profiles on the market, powered by GlobalData. Save hours of research. Gain competitive edge.
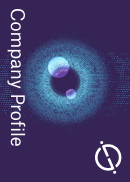
Thank you!
Your download email will arrive shortly
Not ready to buy yet? Download a free sample
We are confident about the unique quality of our Company Profiles. However, we want you to make the most beneficial decision for your business, so we offer a free sample that you can download by submitting the below form
By GlobalDataAbout $US100 million was invested to prepare the plant for the 2005 Dakota. A few years ago, $156 million was invested in preparation for the launch of the 2002 Ram. Add to that another $35 million invested in a third shift and the Chrysler Group has made substantial improvements to upgrade a brownfield site. Those upgrades will allow for rolling vehicle launches and test-build pilot vehicles while not interrupting current model production.
“With these changes, if product strategy calls for a product derivative, then manufacturing is better poised to support the launch of the new model,” said plant manager Bob Bowers. “If the vehicle has the same underbody and a different ‘top hat,’ then it makes it easier for us to build.”
The launch of the Dakota allowed for a restructuring of the plant’s materials handling system to accommodate the greater complexity and variety of parts. Parts are now shipped in small, pre-configured, pre-sequenced lots and delivered to the plant floor in small batches, better utilising floor space and allowing for greater options available to customers.
The launch team also implemented a “Protect the Customer” (PTC) line, which is an additional vehicle inspection line focusing on customer touch points and potential process defects. Issues discovered in the PTC are tracked back through the system for corrective action and future prevention. Warren Truck is one of many Chrysler plants that has implemented this type of initiative, ensuring that only the highest quality vehicles are being delivered to customers.
Third-Shift Success
Warren Truck began operating its third shift last May. Many hurdles were overcome to implement one of the smoothest launches in the group, in part due to advanced preparation and over 80,000 hours of employee training.
Warren was designed to be a two-shift operation with little unused space for an expansion to accommodate a third shift. Due to close collaboration between management, the United Auto Workers union and the entire plant workforce, the facility built the required production volumes on the first day the shift launched and has continued to operate smoothly since that time.
In addition, the employees, on their own initiative, addressed the issue of transitioning between shifts, eliminating the need to shut the line down as is typical in most assembly plants. They created a “buddy” system that requires each employee to arrive 15 minutes ahead of their shift to start work on the line while the other employee finishes a job. Because the employees had ownership of this process, it was adopted easily on all three shifts.
The success of the third shift can be measured in a number of ways, but one of the most important is in employee morale. Now with three eight-hour shifts and no extensive overtime, the workforce is less fatigued, which has resulted in a nearly 5% decrease in absenteeism and better quality metrics than the original two-shift operation.
Warren Truck Assembly produces the Dakota Regular, Club and Quad Cab pickup trucks and the Ram 1500 series Quad Cab. A third model rebadged for Mitsubishi will be added to the assembly line next year.