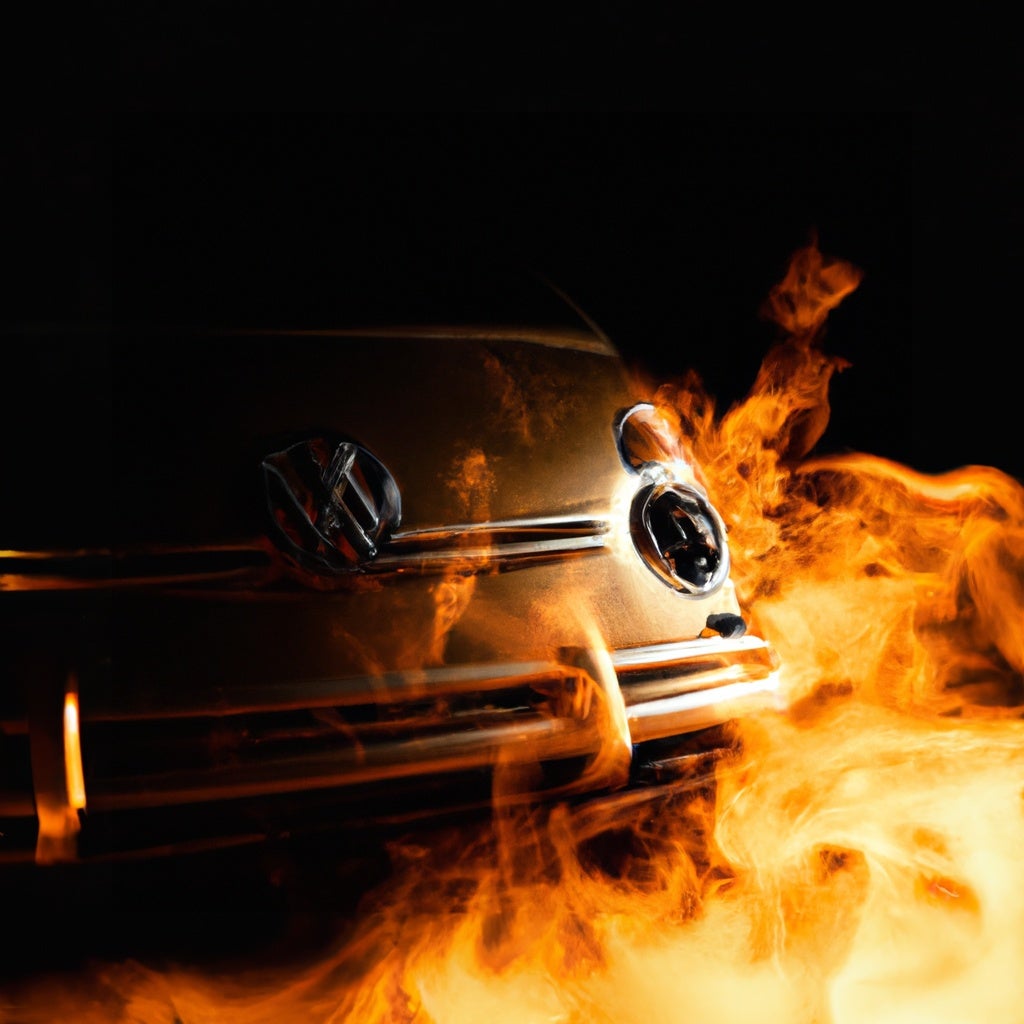
The automotive industry is undergoing a significant transformation, driven by the need for safer and more sustainable materials. According to GlobalData research, a quarter of global light vehicle sales in 2025 are expected to be plug-in electric, highlighting the increasing role of advanced materials in supporting this shift.
As environmental regulations tighten in major markets around the world – recently proposed EU legislation sets targets to cut CO2 emissions from cars by 55% and vans by 50% by 2030 – makers are also seeking alternatives to traditional materials right across the manufacturing process. These materials, while effective, often come with environmental and health concerns; they may cause toxic emissions when burned and face challenges in recyclability.
One of the leading innovations in this space is the development of advanced thermoplastic materials, such as T4, a high-performance resin from Mitsubishi Chemical Group’s TEFABLOC range. A cutting-edge solution, it provides manufacturers with a sustainable alternative to traditional crosslinked solutions, like silicone rubber or XLPE. TEFABLOC T4 is providing a template for materials that can both meets strict fire safety standards and keep environmental impact to a minimum – all while maintaining excellent durability, flexibility, and ease of processing. As the demand for electric vehicles grows – and high-voltage automotive wiring with it – the need for reliable, high-performance and sustainable materials has never been more pressing.
The Advantages of TEFABLOC T4 – why it stands out
TEFABLOC T4 is changing the game in the automotive material world due to its combination of fire resistance, ease of manufacturing and sustainability. One of its defining properties is its outstanding flexibility even at low temperatures. This is critical for automotive applications where cables must perform reliably – often in harsh environments, including sub-zero temperatures. “Flexibility at low temperature is very important compared to previous solutions,” says Charles Olivier Aubin, global product manager for the FRPO product range at Mitsubishi Chemical Group. “This ensures the wiring remains intact and functions optimally, reducing the risk of cable damage over time.”
Another significant advantage of TEFABLOC T4 is its recyclability. Unlike existing solutions, which are difficult or impossible to recycle, TEFABLOC T4 is fully recyclable. Traditional silicone rubber and XLPE requires a cross-linking process that makes it challenging to break down and reuse. In contrast, TEFABLOC T4, as a thermoplastic material, can be melted down and reformed, significantly reducing waste. This recyclability aligns with the automotive industry’s increasing focus on sustainability and circular economy principles. It allows manufacturers to reduce their environmental footprint now – while futureproofing them against new sustainability regulations coming down the track.
TEFABLOC T4 also offers lower energy consumption during the cable manufacturing process. The processing steps required when working with XLPE and silicone materials can consume considerable amounts of energy. TEFABLOC T4, by contrast, eliminates these energy-intensive steps, allowing manufacturers to streamline production while reducing costs and carbon emissions. “With the T4, customers can use the compound directly in extrusion and produce cables in just one step,” Charles Olivier Aubin explains. “This is not the case for silicone or XLPE, which require additional post-treatment and specific machinery.” Additionally, its throughput dwarfs that of its nearest competitors – meaning users get significantly greater outputs when manufacturing with TEFABLOC T4 from the same energy inputs.
Beyond its process efficiency, the TEFABLOCrange from which T4 originates offers several benefits that make it an optimal choice for demanding applications. This range is known for its flame and heat resistance, cold flexibility, scratch resistance, and ease of processing. Unlike both silane and e-beam cross-linked solutions available, TEFABLOC T4 provides enhanced properties tailored to specific industry requirements.
Partnering for Success
With the rapid evolution of materials science and sustainability requirements, automotive manufacturers must work closely with trusted partners to deploy the most advanced and reliable solutions. Mitsubishi Chemical Group, a leader in high-performance materials, has positioned itself at the forefront of this transformation with its innovative TEFABLOC T4 range, including OLEFISTA.
Collaborating with an established supplier ensures manufacturers can leverage deep industry knowledge and R&D capabilities to meet evolving regulations and performance demands. It also allows for tailored material formulations optimised for specific applications, ensuring compliance with the latest automotive standards and futureproofing them against change. Furthermore, working with a company that prioritises recyclability and low-energy production helps manufacturers both shore up performance and meet and exceed sustainability goals.
“More and more, companies are looking for solutions that not only meet technical requirements but also reduce their environmental footprint,” notes Charles Olivier Aubin. “This is where TEFABLOC T4 and the OLEFISTA range stand out—offering easy processing, limited upfront capital costs, and compatibility with standard manufacturing equipment, ensuring manufacturers can transition smoothly without major infrastructure changes.”
As the automotive industry continues to push for safer, greener, and more efficient materials, T4 presents itself as a future-proof solution. Its balance of fire resistance, flexibility, recyclability and energy efficiency makes it a leading choice for next-generation automotive wiring and cable applications. The Mitsubishi Chemical Group is the manufacturers’ premium partner in the EV revolution, keeping efficiency and performance at the heart of vehicle performance. For further information, fill in your details on this page.