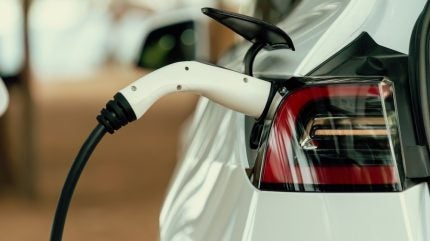
The move towards electric vehicles (EVs) is gathering momentum and production is increasing. According to analytics group GlobalData, by 2028, the global EV market will see a compound annual growth rate (CAGR) of 16.1% to reach 53.9 million units. Battery electric vehicle (BEV) production is set to overtake hybrids, becoming the leading electrified driving option on the market by the end of this period.[i]

This rapid growth in BEV volumes is a clear indication of the major shift underway in the automotive industry, as it transitions away from traditional internal combustion engine vehicles (ICE) towards cleaner, battery-powered electric vehicles.
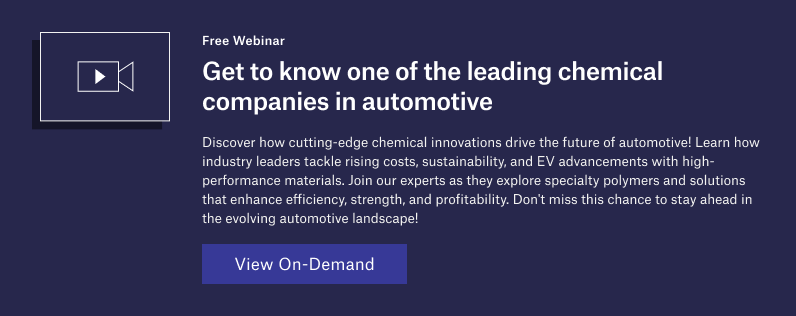
However, the rising EV volumes underscore the importance of addressing safety challenges, like fire risks, as electrification technology becomes more widespread.
Evaluating risk: the rocket test
The ‘rocket test’ is a testing method used by Mitsubishi Chemical Group to evaluate the performance of battery enclosure materials under conditions that simulate a real-world battery fire.
The goal of the rocket test is to expose materials to severe conditions typically experienced during a cell burst event, namely extreme flame temperature and jet force, the latter which is often missing in other standard testing methods. The test generates a focused high-velocity flame that includes particles directed towards the material that in turn must resist the combination of extreme temperature, particles, and kinetic energy and not allow flame break-through. The test parameters are based on cell burst experimental data and closely replicate real world flame temperature and jet force. Sensors are used to record force and temperature during the test. Additionally, the test is rapid, customizable, highly repeatable, and cost-effective, making it an ideal R&D tool for material development and verification.
In a recent webinar, Fire safety in the EV era: materials, processes, and firms driving change, Mitsubishi Chemical Group’s Leonard Lichtblau discussed how the rocket test is making a valuable contribution to fire safety.
“You can simulate the cell burst damage caused by the jet flame,” explains Lichtblau. “It is repeatable, stable, rapid… much more than using real cells. You can do 8-10 tests in a day, no problem. It’s also cost effective, compared to tests with real cells. It’s an exceptionally good R&D screening tool which helps us to optimise our materials for use in battery enclosures. We have already completed six campaigns with over 80 tests on four of our composites material families.”
According to the Mitsubishi Chemical Group (MCG), major global automotive OEMs are already implementing the rocket test as a mandatory testing specification for battery enclosure materials. Its acceptance within the industry is clearly becoming more commonplace, allowing MCG and its customers to develop safer and more effective battery enclosure materials.
Solutions: polymer composites
While the causes of thermal runaway are well known, solutions have been harder to establish. Some solutions include optimised lightweight polymer composite materials for enclosures and covers, such as MCG’s KyronTEXTM – a fiber-reinforced thermoplastic composite that excels in the rocket test, where it outperformed most tested materials, including metals and thermoset composites such as SMC. Thus, additional fire protection materials typically used in battery enclosures, such as mica, become unnecessary resulting in cost savings with increased performance. These advanced lightweight polymer composites are designed to withstand the intense heat, pressure, and debris from a battery fire, helping to contain the thermal runaway event.
In addition to the enclosure materials, the use of MCG’s Thermal Control Material Spacer THERMINSYNX™ can limit thermal propagation, by isolating a failing cell and preventing the fire from spreading to the rest of the battery pack. They promote heat transfer within the pack when the cells are operating normally and suppress the spread of fire when a thermal runaway occurs. They also exhibit excellent compression properties in response to the expansion and contraction of the cells, which contributes to improving the battery energy density and extending its lifespan.
The key is addressing the unique challenges posed by the high-energy nature of lithium-ion battery fires, requiring innovative materials and testing approaches beyond traditional flammability assessments. MCG has worked closely with major OEMs to validate these solutions, ensuring they meet the specific requirements and safety standards of the automotive industry.
Speaking on the same webinar, Matt Orlando, Automotive Market Director, Mitsubishi Chemical Group, described some of the other developments Mitsubishi is involved in.
“With the help of Dr Leo Lichtblau and other scientists, we have found a variety of materials that enhance, and make more efficient, current battery systems,” he says. “We have materials that can be used for potting materials, coolant tubes, [thermoplastics] like PBT which is used in a variety of connector and wiring materials. We have battery case and tray materials and are one of the largest suppliers of anode and electrolyte materials for lithium-ion batteries in the world.
“We also have a thermal spacer material, which is highly innovative under normal conditions. It is thermally conductive, so it keeps one cell from being hotter than the rest. It transfers energy, ensuring you can avoid situations where one battery heats up and damages others. It also extends the life of the battery by keeping them at very low temperatures.”
Looking ahead
Over the next decade, there are several challenges the EV industry will need to address. MCG’s experts concluded the webinar by zooming in on the most critical.
First, the development of no thermal propagation (NO TP) batteries. Battery cell design and chemistry must limit thermal runaway to a single cell or a maximum of two cells. The goal is to prevent thermal propagation through the entire battery pack – a significant safety concern. And, on top of cell-level improvements, there is a focus on developing ways to better isolate individual battery cells within the pack.
Second, evolving regulations and standards. The regulatory environment around EV battery safety is still quite fragmented globally, with different standards and requirements emerging in various regions. Automakers and suppliers will need to adapt to these evolving and potentially more stringent safety regulations.
Third, continued material innovations. Companies like Mitsubishi Chemical Group are positioning themselves to tackle safety challenges through continued development of advanced materials for battery enclosures, thermal management, and other critical components.
Finally, collaboration across the industry. Addressing safety challenges will require close collaboration between automakers, battery suppliers, material providers, and other stakeholders. Sharing knowledge, testing methods, and innovative solutions will be crucial as the industry works to improve EV safety.
Orlando concluded the webinar with this thought: “We have 1000s of research scientists around the world who are there developing new opportunities, trying to help simulate scenarios and provide solutions, not just for our customers, but for the world at large.” With Mitsubishi Chemical Group a global leader in making the EV transition safe, manufacturers big and small must take note of their transformative role and the value of a collaborative partnership. Fill in your details to find out more.
[i] GlobalData: Automotive Predictions 2024, January 2024, page 4