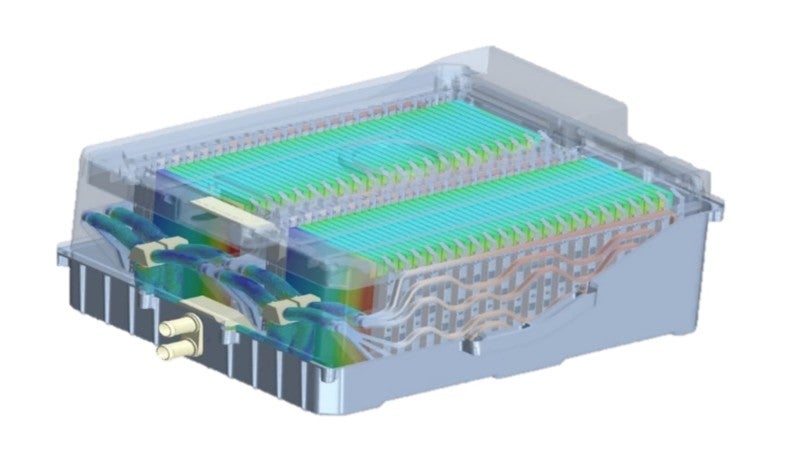
Before the battery team can release a final pack design to the body in white (BIW) team to integrate into the car body in a way that meets the overall vehicle structural, noise, vibration, and harshness (NVH) and weight targets, it must be verified whether the battery pack meets all the thermal and energy requirements.
This stage includes the following steps:
• Pack thermal management optimization.
• Battery pack thermal runaway analysis to ensure a graceful failure.
• Validation of battery energy and thermal performance against vehicle requirements.
• Battery management system (BMS) embedded software development and validation.
Thermal management optimization is conducted to ensure cell-to-cell temperature variation, to maintain maximum temperature within specification, and to verify that the battery pack meets all thermal and energy requirements. Engineers use computational fluid dynamics (CFD) simulation solutions to optimize thermal management strategies, ensuring it meets requirements for critical operation scenarios.
The design must ensure what is called a “graceful failure” to avoid fire in the event of one or more cells failing. Safety considerations include ways to limit temperature spikes in a significant number of cells if one cell in the package undergoes a thermal runaway event. Another hazard that must be considered is the spread of battery pack gases that may vent into the cabin. Slowing the spread will allow time for passengers to exit the vehicle.
Battery pack safety testing is critical; however, it does not explain why a design may fail. Pack safety simulations offer insight on where limitations might be found and how to address any operational issues, thereby strengthening the design process.
Large battery pack safety testing is challenging. Safety simulations that account for chemical reactions, transient temperature spread, and the details of pack layout geometry are vital to ensure a safe operation. It is also critical to assess the impact of any pack geometric changes to satisfy thermal performance on vehicle integration and packaging.
Battery pack validation
Once the thermal management of the battery pack has been optimized the EV teamwork with the systems engineers to validate the electrical and thermal performance of the battery pack within the complete vehicle system. Only then is the battery pack design fixed.
For this collaboration, a digital continuity and integrated workflow between detailed three-dimensional (3D) battery pack design analysis and one dimensional (1D) vehicle system analysis is used. Central to the success at this stage is bringing battery-specific analysis to system simulation without slowing down computation. Extracting reduced order models (ROM) and integrating it into a system simulation achieves a massive increase in speed.
This integrated 1D-3D workflow allows engineers to validate drive range for a complete drive cycle with realistic power demand, including demands from cabin cooling and other auxiliary power. Engineers can also reliably estimate change in range at different ambient temperatures.
Developing the brain
The battery management system (BMS) is the brain of a battery pack and can be developed at the same time as the pack’s mechanical and electrical systems are being designed. there are four key elements for BMS algorithm and software engineering:
1. Software requirement management and process orchestration for development and validation.
2. Accurate algorithms to estimate state of charge, state of health, remaining drive range, as well as algorithms for cell balancing and thermal management are developed. These algorithms need to account for cell chemistry and performance.
3. Algorithms then need to be transformed into embedded software. Poorly architected software introduces errors that cause recall and liability risks. Once the software architecture is designed, embedded software integration needs to ensure AUTOSAR implementations, generating real time executables (RTEs) and cyber security.
4. Extensive testing of BMS is critical. Engineers increasingly rely on Software-in-the-loop (SiL) and Hardware-in-the-loop (HiL) testing to validate BMS software before release.
The ability to update BMS simulation with a new model reflecting any battery pack layout design changes benefits design efficiency. The goal of this stage of the process is a verified, signed-off battery pack design.